Common Issues and Solutions in Sheet Metal Fabrication
In sheet metal fabrication, encountering various issues is common. These problems can affect product quality, processing efficiency, and even increase production costs. Understanding the root causes of these issues and implementing appropriate measures is crucial for any sheet metal fabrication shop.
Table of Contents
Material Deformation
Material deformation often occurs during welding and cold processing. In welding, uneven heat distribution can cause the material to expand and contract, leading to deformation. Similarly, during processes like stamping or bending, if the pressure is uneven or the material thickness is inconsistent, deformation can also occur. To avoid these issues, materials can be preheated before welding to reduce thermal stress, and pressure on cold processing equipment can be adjusted to ensure uniform stress distribution on the material.
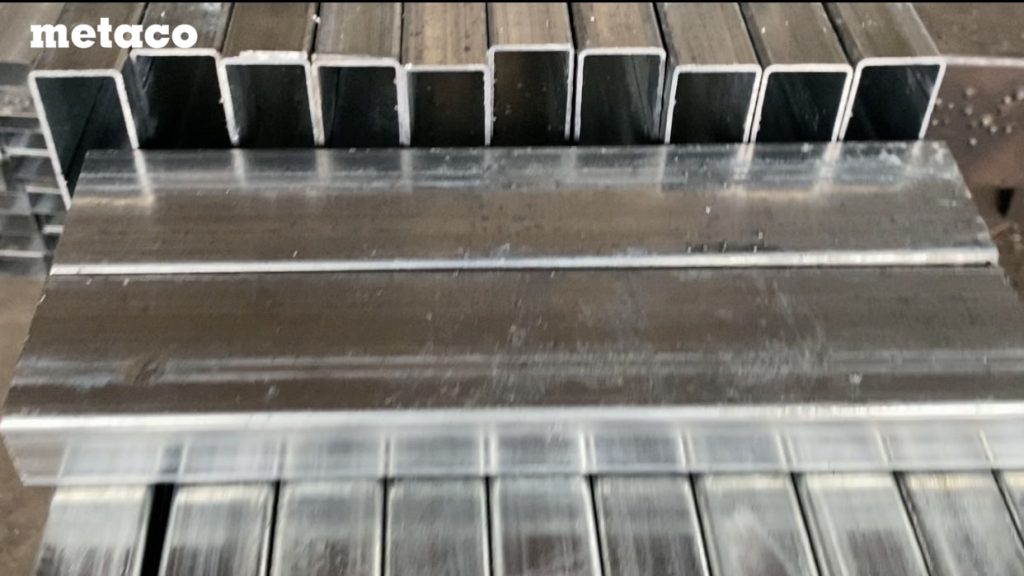
Cutting Precision Issues
Sheet metal cutting requires high precision, and if the cutting precision is not up to standard, it can affect subsequent processes. A common reason for this issue is tool wear. When cutting tools become dull, they cannot maintain precise cuts. Additionally, improper equipment settings or operator errors can also lead to dimensional inaccuracies. Therefore, it is necessary to regularly check and replace cutting tools, calibrate the equipment accurately, and adjust cutting speed and pressure as needed.
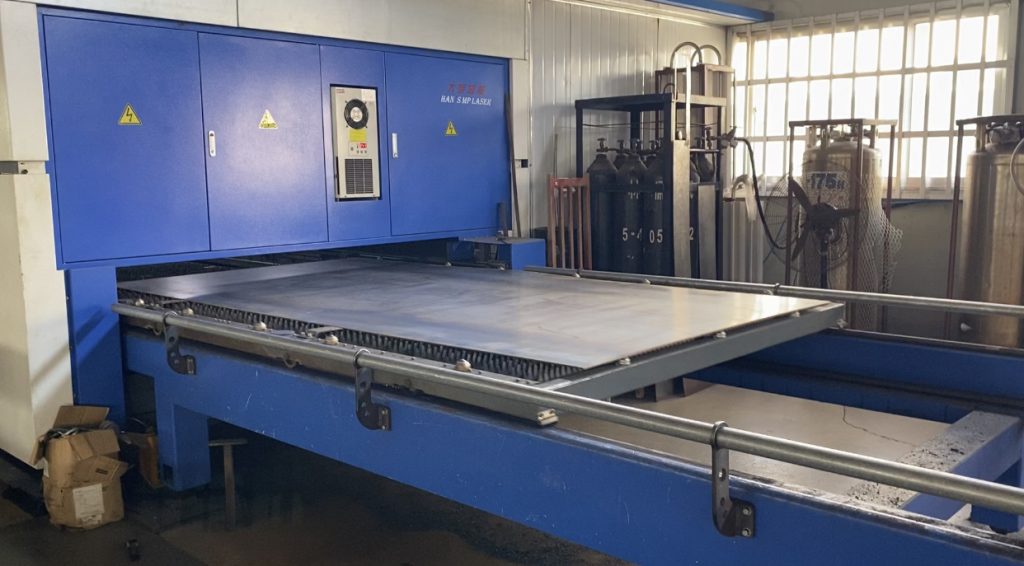
Insufficient Weld Joint Strength
Insufficient weld joint strength is another common issue, often related to welding methods and material selection. If the welding process is not suitable or the welding material does not match the base material, the weld joint may not meet the expected strength. To prevent this, the chosen welding method must align with the material characteristics, and the welding materials should be compatible with the base material. Additionally, controlling the temperature and speed during welding can ensure strong weld joints.
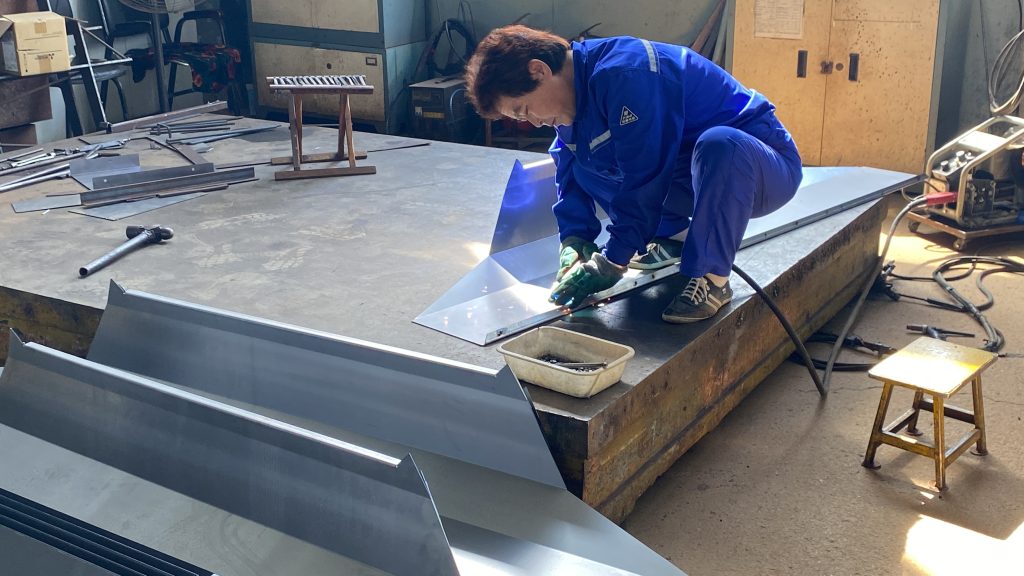
Surface Quality Issues
Surface quality is crucial for both the appearance and functionality of sheet metal products. During cutting, burrs are often left behind, welding can cause spatter, and bending may result in surface defects if the die alignment is inaccurate. To prevent these issues, burrs left from cutting should be promptly removed, and welding spatter can be cleaned through grinding or polishing. Furthermore, ensuring precise die alignment during bending helps avoid surface defects caused by equipment problems.
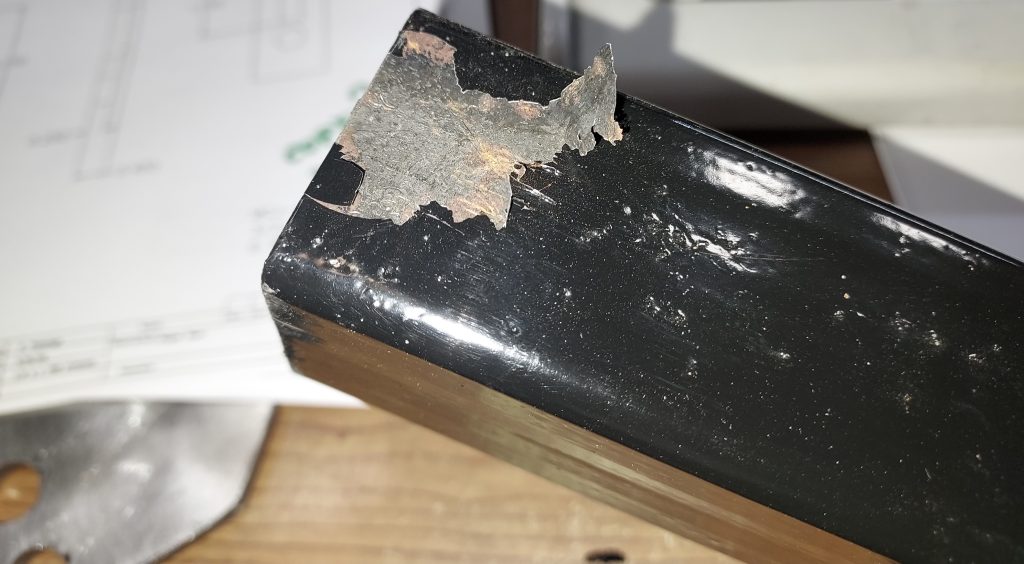
Cost Overruns
Cost control in sheet metal fabrication is a significant challenge. Production costs often exceed expectations due to improper process selection, inefficient equipment, or incorrect material choices. In this regard, it is essential to carefully select processing methods and materials, avoiding complex and high-cost techniques. Additionally, increasing equipment production efficiency and adopting automated production lines can reduce labor costs and help effectively control overall expenses.
These issues are common in sheet metal fabrication, but they are not insurmountable. By continuously optimizing processes, selecting the right materials and equipment, and addressing problems early, manufacturers can ensure smooth production, improve product quality, and reduce production costs.