Materials For Metal Stamping
Material choice is critical in stamping, as it directly impacts the quality of the final product and the efficiency of the production process. The ideal stamping material balances performance with cost, tailored to meet the specific demands of the product and the stamping technique used.
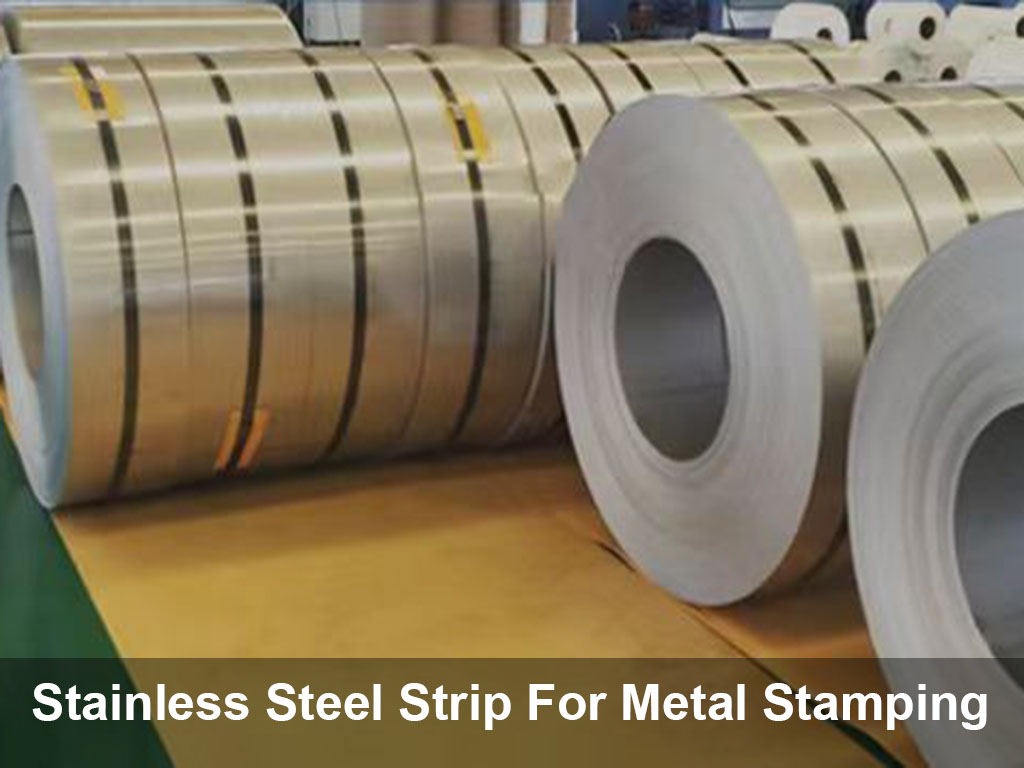
Common Stamping Materials
Steel Stamping
Brass and Copper Stamping
Aluminum Stamping
Magnesium Stamping
Stainless Steel Stamping
Material Selection Factors for Stamping
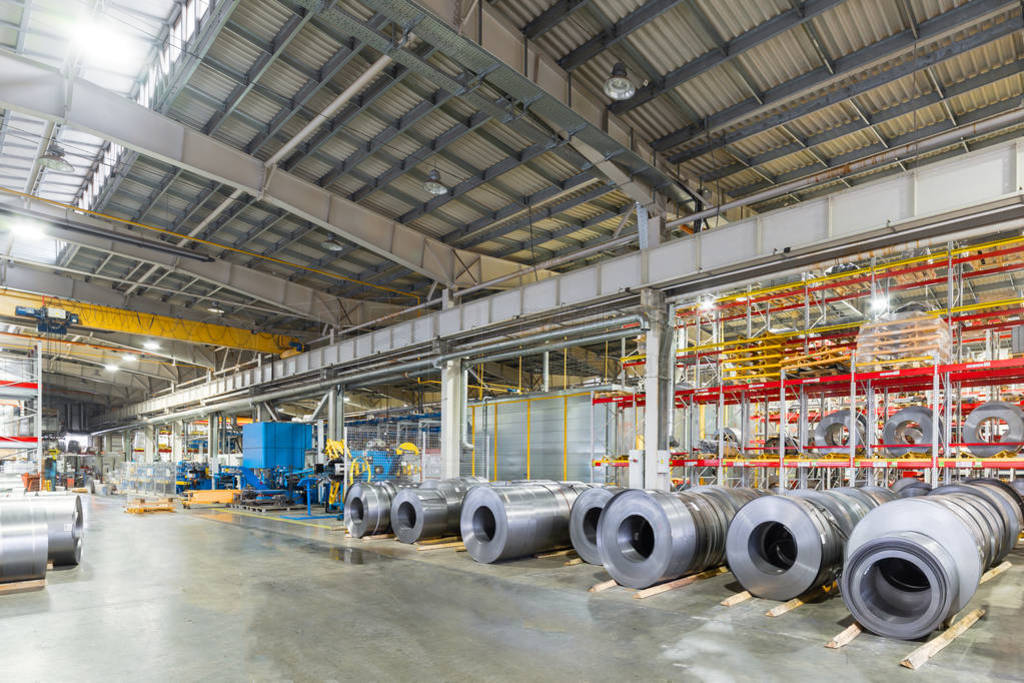
Based on Stamping Process
Materials must form parts without cracking or wrinkling, meeting the fundamental criteria for stamping.
Trial Stamping
Perform trial runs with materials that initially meet the requirements. Choose the material that shows no cracks and has the lowest rate of defects.
Analysis and Comparison
Compare the maximum deformability during stamping with the material’s limit of deformation allowed, based on an analysis of the material’s stamping properties.
Based on Usage of the Stamping Parts
Choose materials that meet the necessary strength, stiffness, toughness, corrosion resistance, and heat resistance required by the operating conditions of the parts.
Based on Cost-Effectiveness
Consider cost differences among materials. More affordable materials can reduce manufacturing costs but may compromise mechanical properties and machinability. Weigh the trade-offs between cost and performance to find the most economical choice.
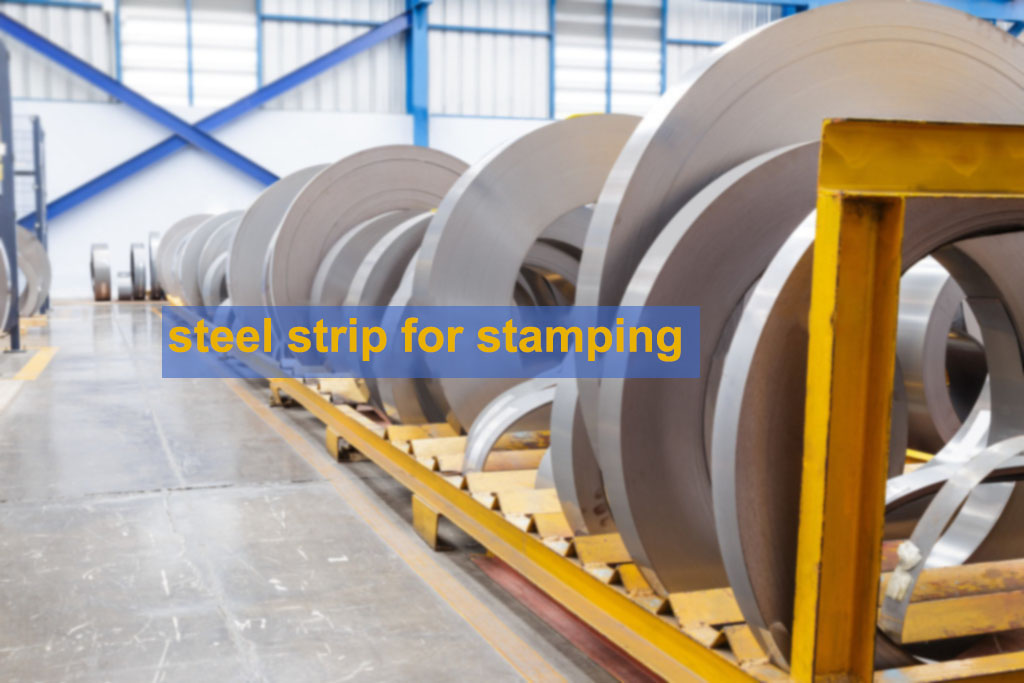
Surface Treatment After Stamping
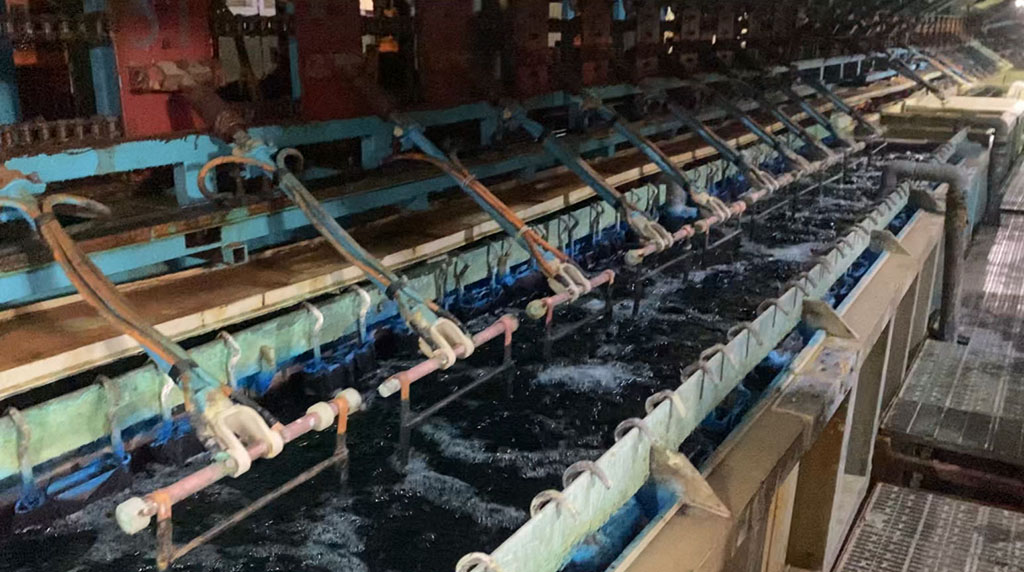
galvanization
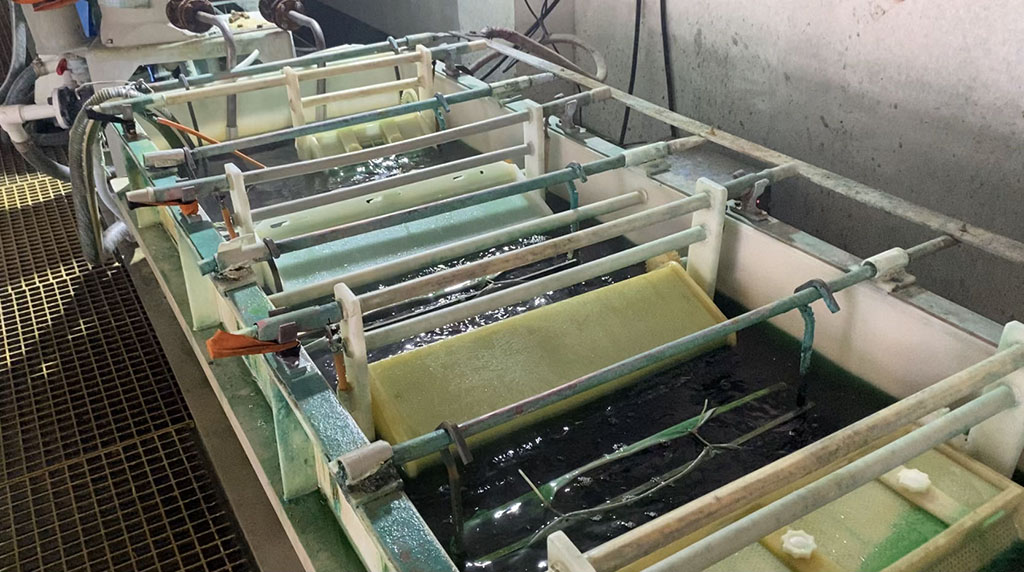
electrodeposition
Stampings in different materials
Heat Exchanger Tab
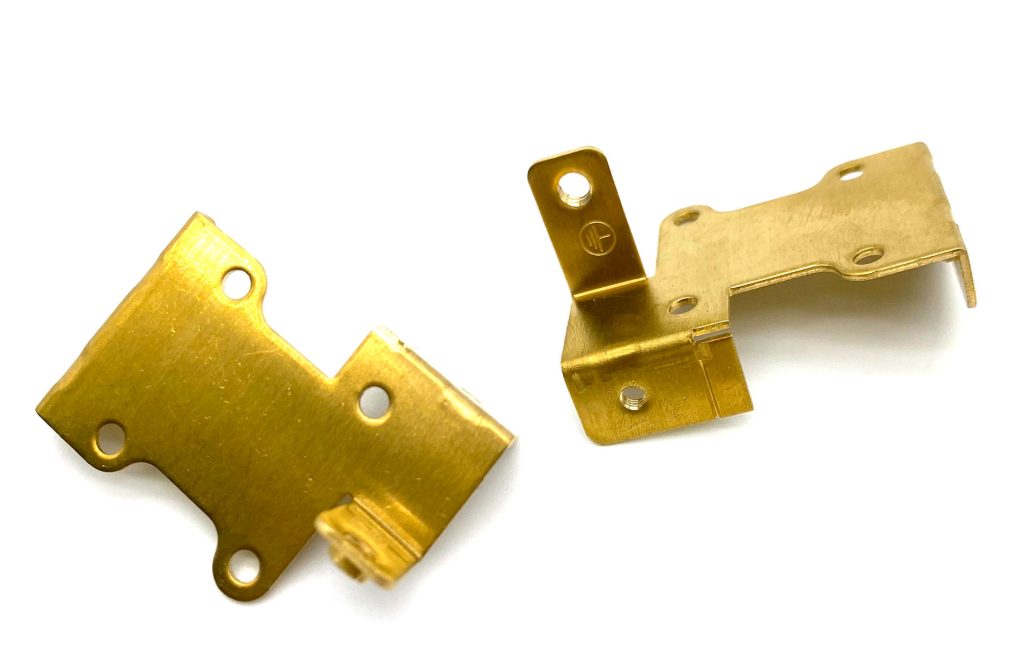
Brass
Bottle Cap For Packaging
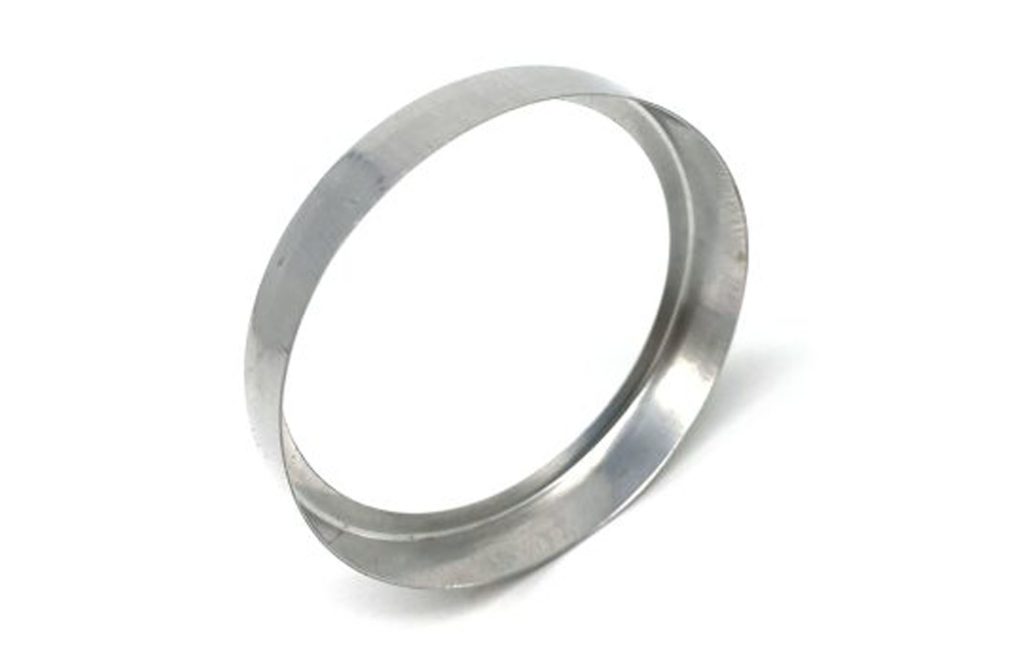
Aluminum
Speargun Shaft Flopper
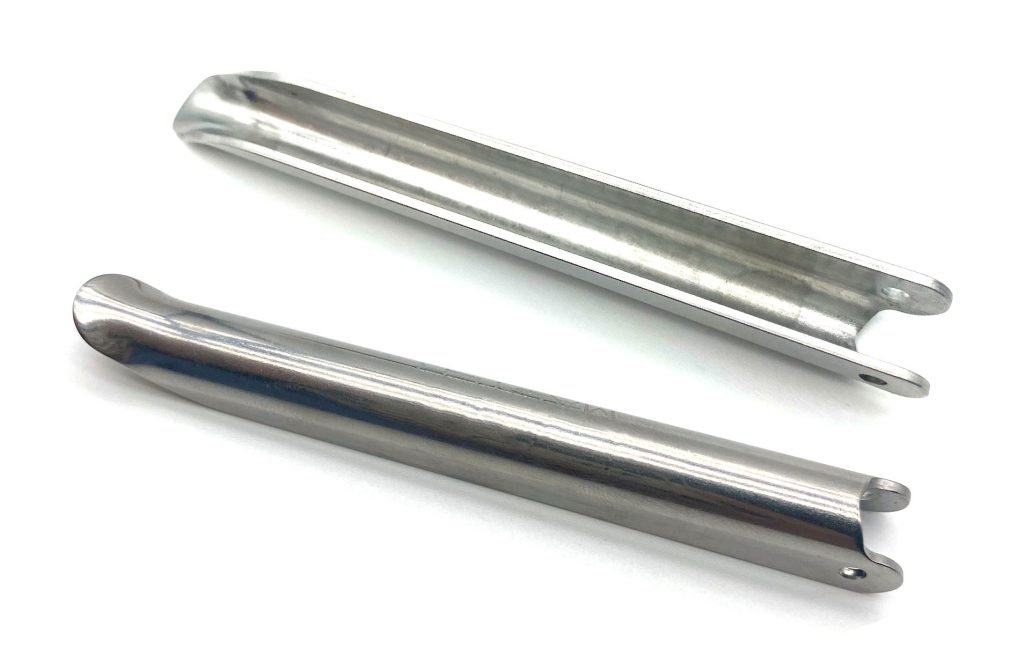
SUS304
Floor Reinforcement Cover
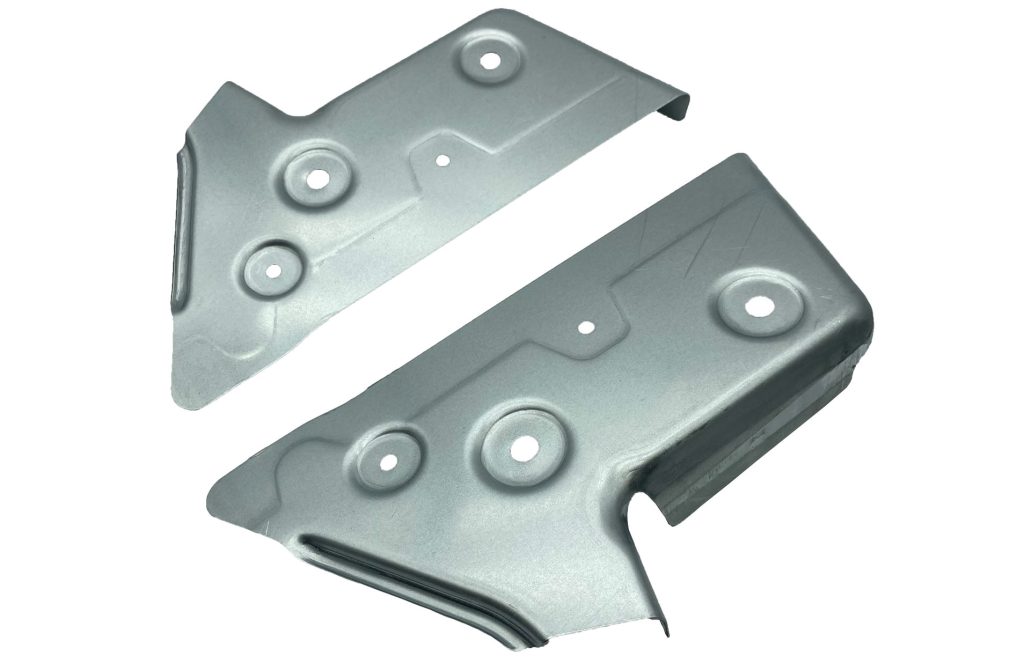
SECC
Reflector Plate R Front
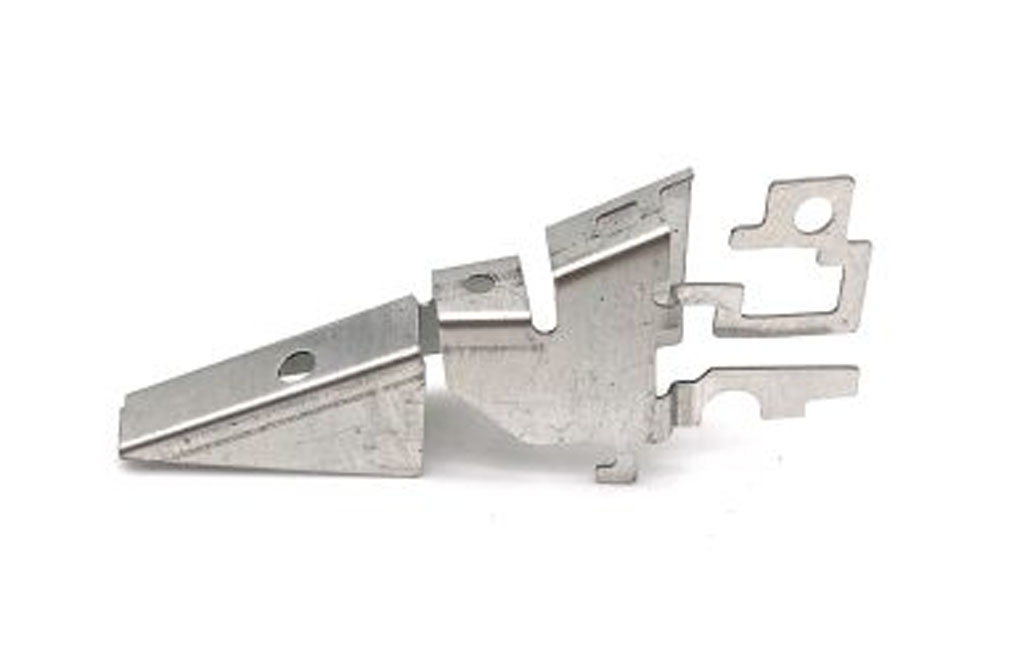