Metal Fabrication Quality Assurance
Typically, every metal fabrication product with us goes through a process of sampling, small orders, and then larger orders for validation. The chances of quality issues arising later on are very low. But let’s face it, in any production process, perfect quality every time is just not realistic. We’re no exception. Because production is a chain of processes, from raw materials to processing, outsourcing, surface treatments, and even packaging and shipping, there are plenty of points where things could go wrong.
Cases of quality issues
Entire Packaging Replaced bue to Label Error
We’ve had experiences, like mistakenly printing the wrong label on an order, leading us to replace the packaging of an entire batch of products. The goods were already at the port, and we had to rush, sending people to replace the packaging with the correct labels. All because of one little label.
Fixing quality issues with goods that haven’t been shipped out yet is relatively manageable. But when it’s products already at the client’s end, discovered to have quality issues, the costs shoot up. So basically, our warranty policy is all-in: we remake the products for the customer. These situations are very rare, but when they happen, we have no choice but to do this.
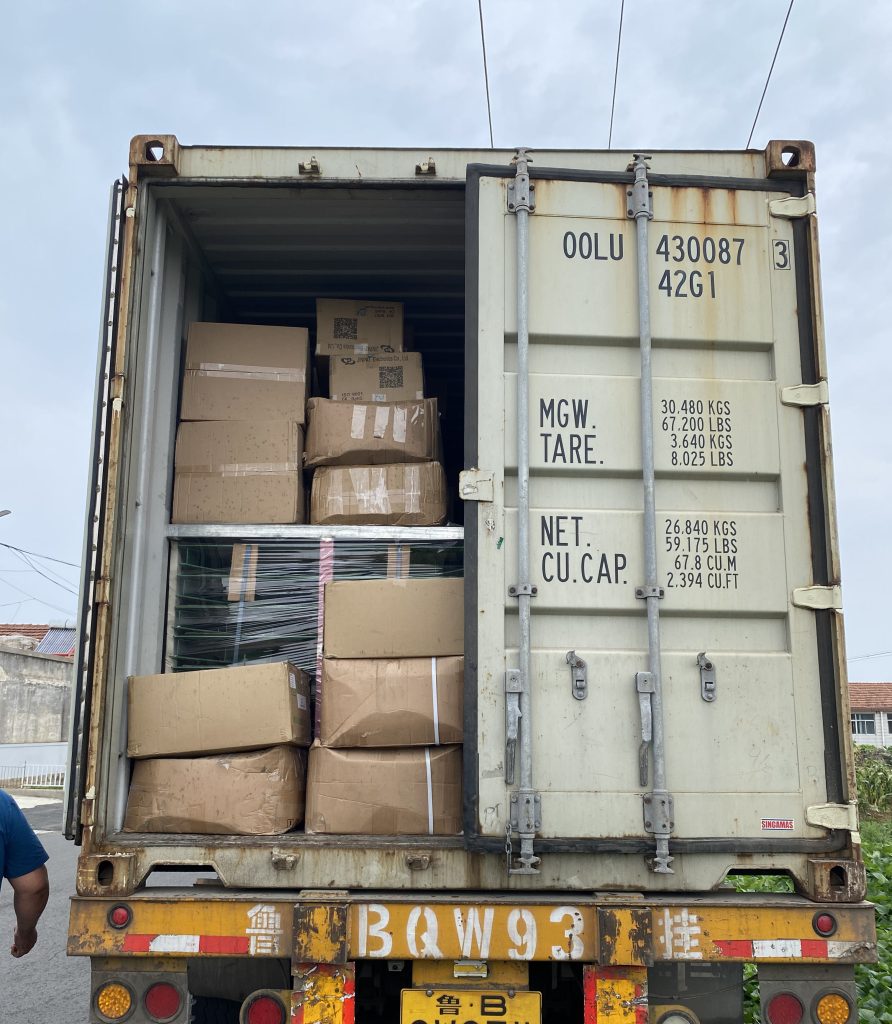
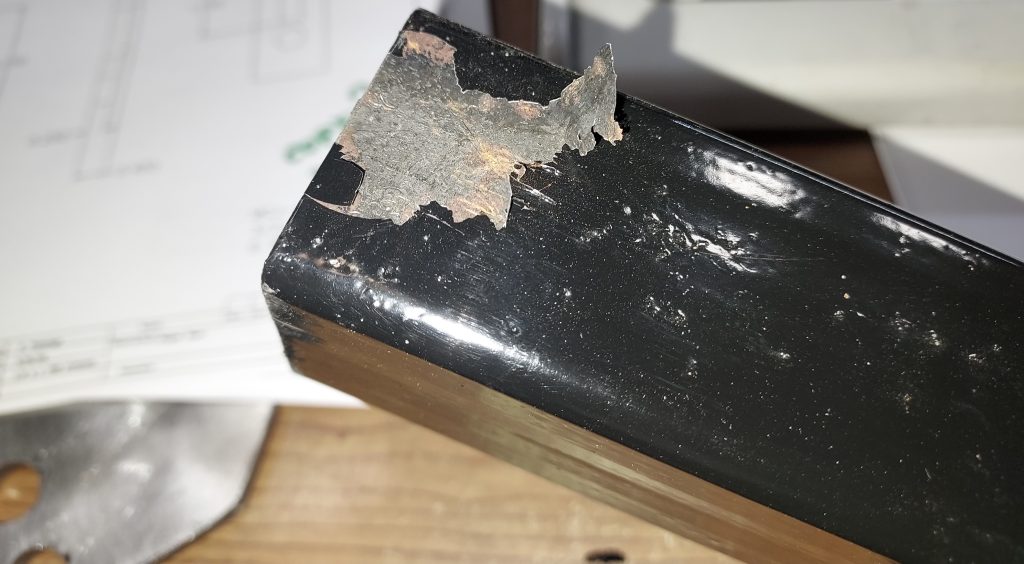
Full compensation For Major Quality Issues
We once faced a quality issue with the coating process due to inadequate pre-treatment. Initially, after the coating was applied and cured, everything seemed fine aesthetically. However, after a period of transportation by sea, when the products reached the client’s location and were inspected, we were shocked to find the coating peeling off like snow flakes, rendering them completely unacceptable. When the client sent photos showing the peeling coating, I could hardly believe my eyes. But after conducting thorough self-inspection in our production process, we identified the root cause of the problem.
The dimensions and welding processes were all fine, and the client only needed to recoat the products for use. And indeed, that’s what the client did. But because the problem originated from our end, our policy is to fully compensate with new pieces – whatever quantity the customer reports as defective, we remake that whole batch and resend it.
Why do we confidently offer this full compensation pledge? Well, firstly, we have a firm grip on our production processes and quality control. Secondly, we’re a responsible metal fabrication supplier. And lastly, it’s about trust – our clients are long-term partners, and we take their feedback seriously. That’s trust.