In-house Stamping tool and die
In-house stamping tool and die is one of the key competences of Metaco custom metal stamping service. We design, manufacture and commission the stamping tool and die in house. With the support of in-house equipment like wire cutting, CNC machining, EDM, surface grinding and related tools, we are able to respond quickly according to customer’s demand or production requirement.
Stamping Tool and die design
Metaco excels in offering comprehensive stamping die solutions. Our in-house team integrates die designers, manufacturers, and assemblers—a rare capability in the industry. This vertical integration, coupled with our extensive stamping experience, streamlines the die design process and ensures quality throughout development, eliminating intermediaries and enhancing efficiency.
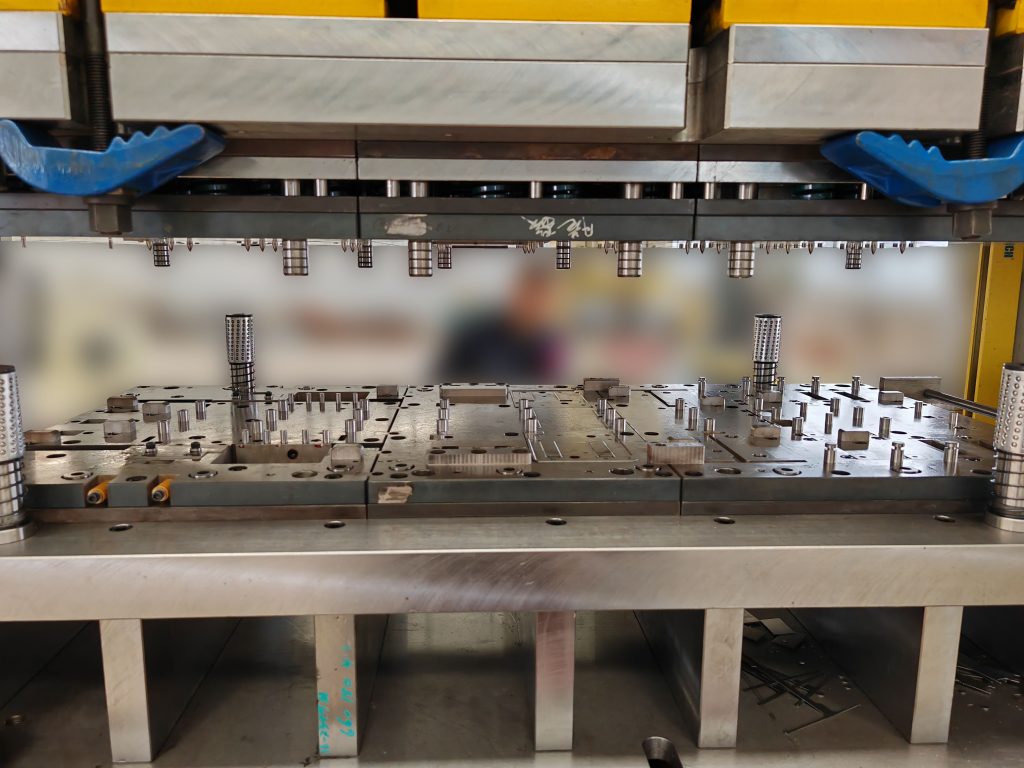
Digital Drafting for Stamping Dies
Stamping Die Simulation for Risk Reduction
Designing the Stamping Die Process
Stamping Tool and die Manufacturing
Die Material
The material is die steel with smooth, precision-finished plates.
CNC Machining
Precision machining for the die’s core structure.
Heat Treatment
Increases hardness and ensures no deformation.
Grinding
Refines the surface for smoothness and accuracy.
Wire Cutting
The most critical step in die manufacturing.
Die Maintenance
Metaco handles die maintenance and repair.
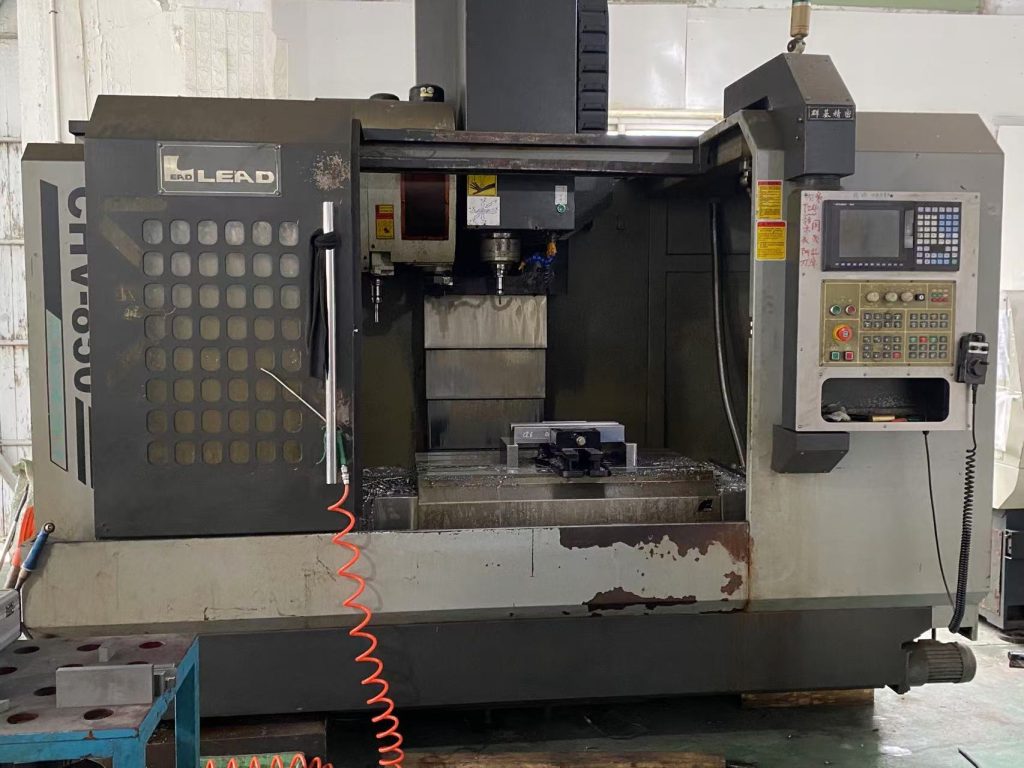
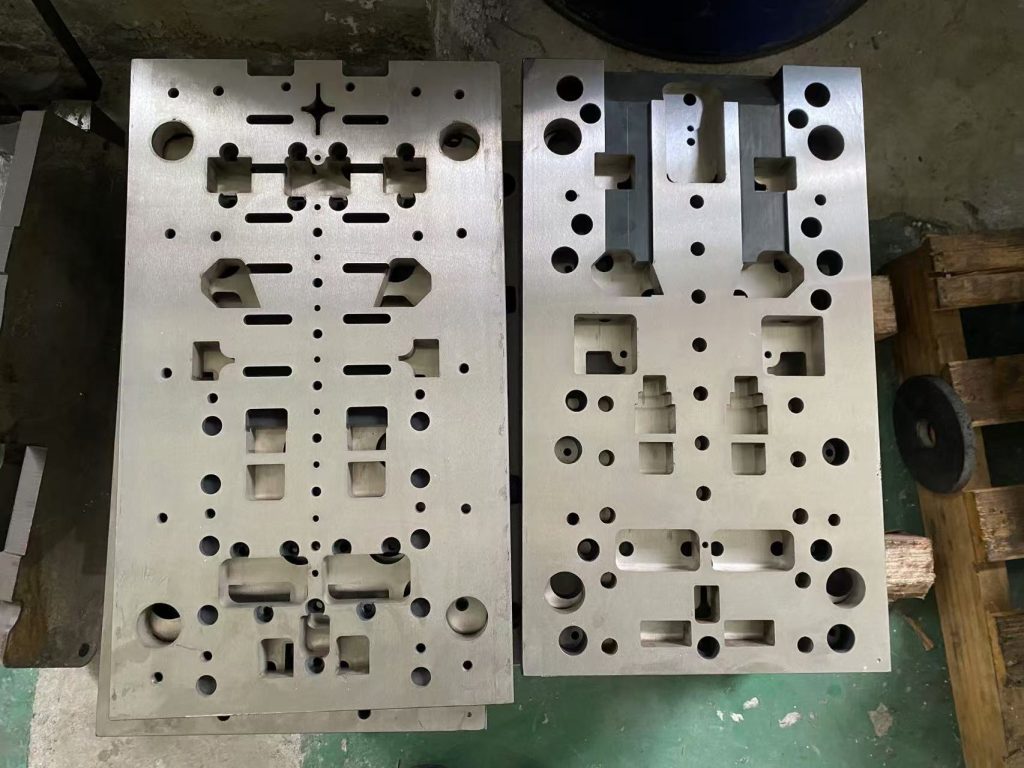
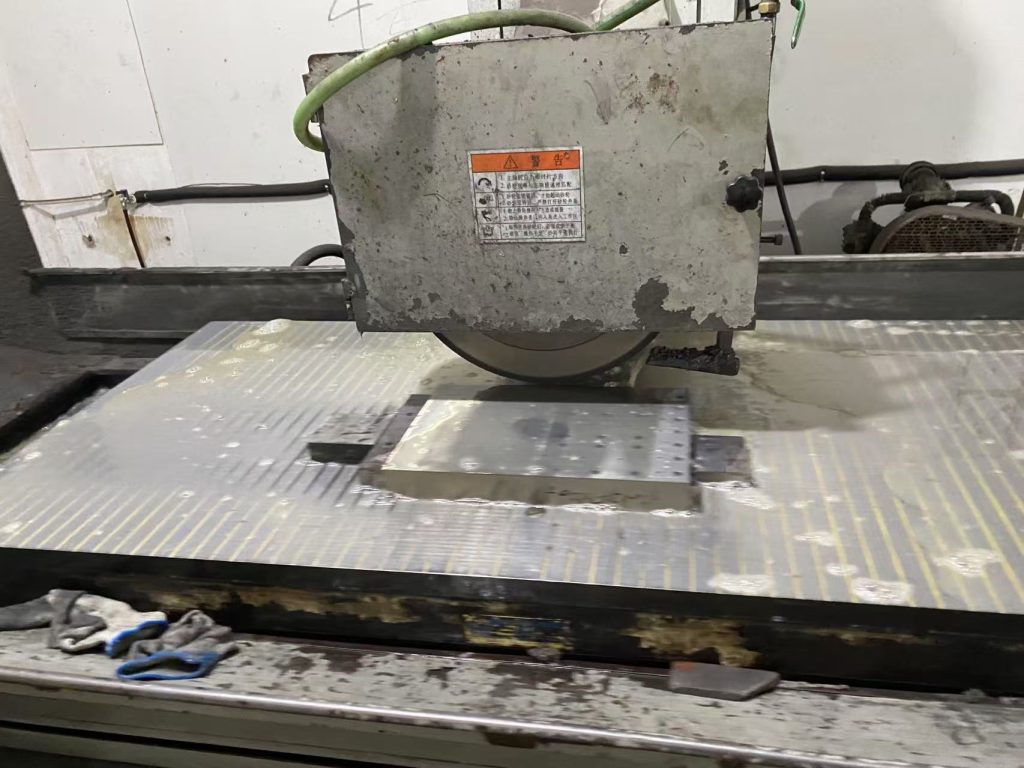
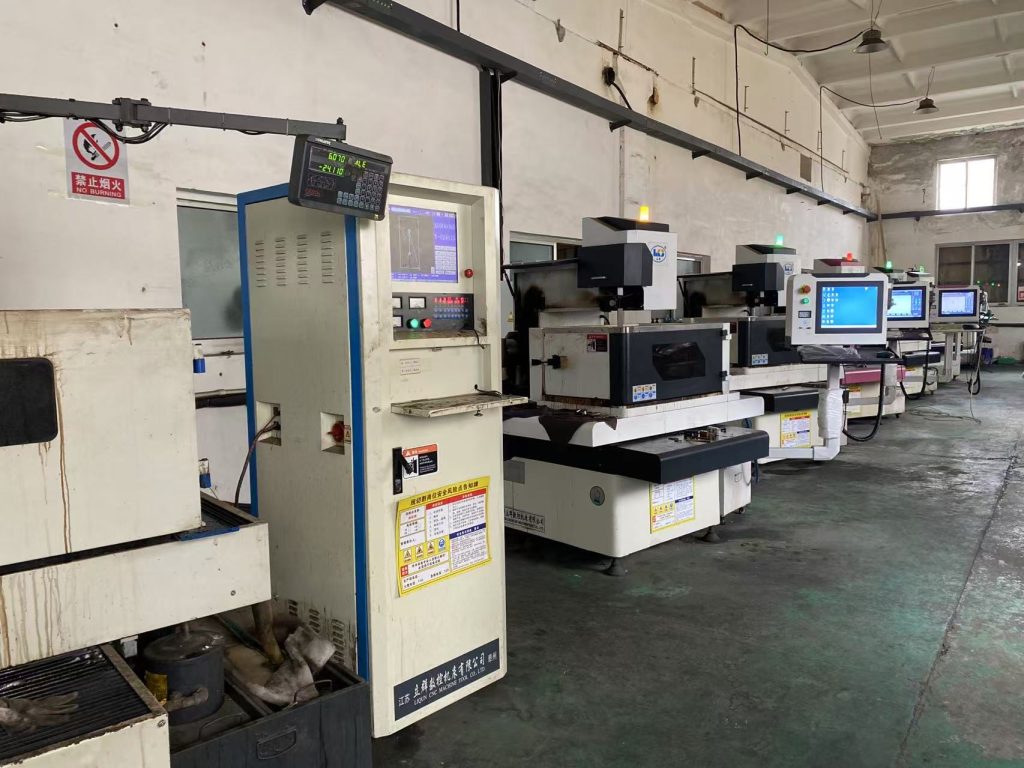
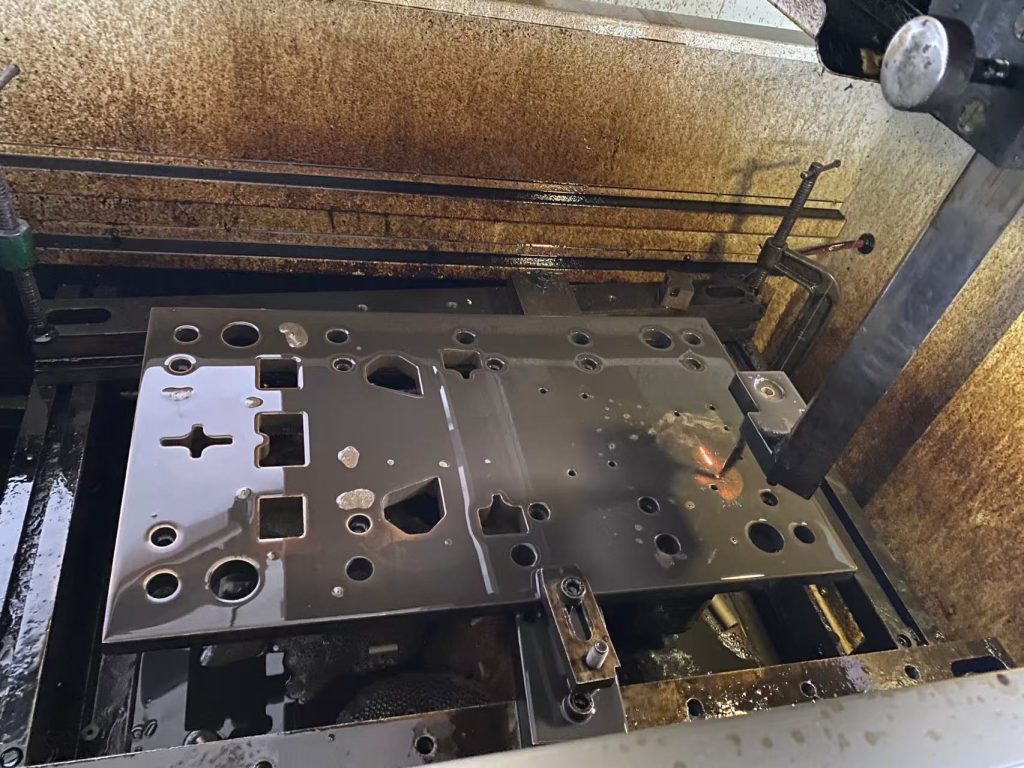
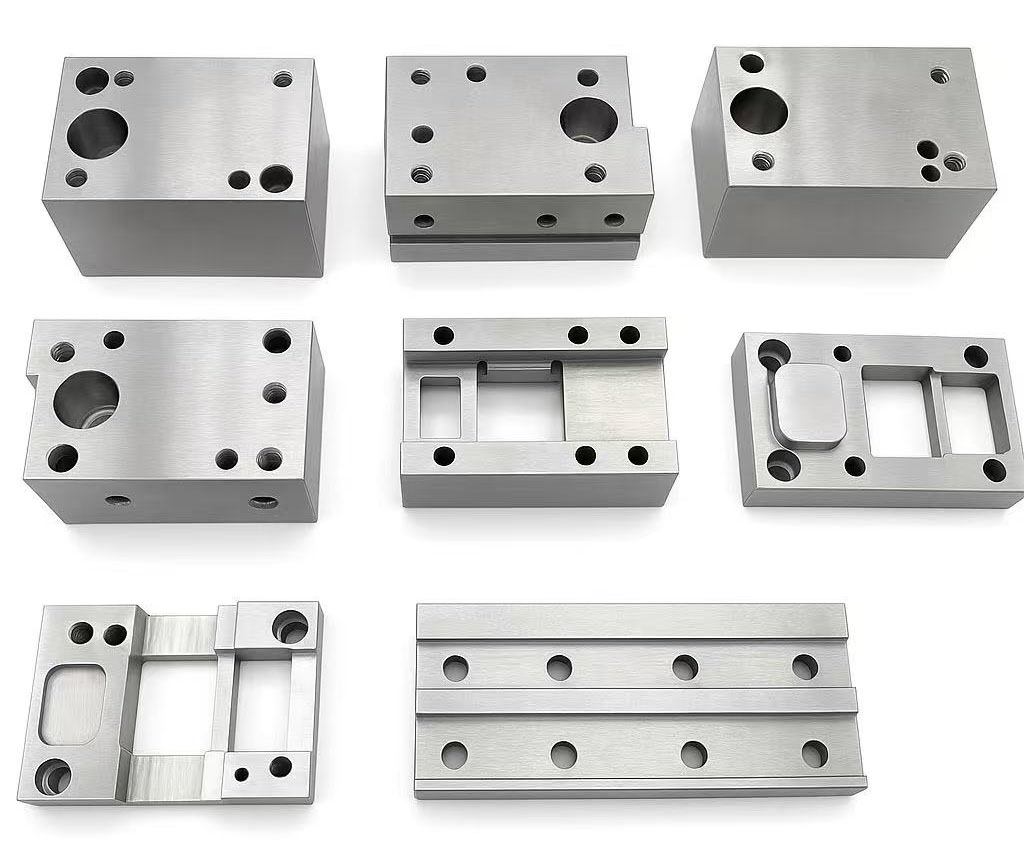
Custom Stamping Die Components Service
Based on customer needs, we continuously enhance our services. Metaco also offers custom processing services for stamping die components, including:
punches
dies
guiding components
ejection plates
We support processing based on provided drawings and offer customization with various materials, including alloy steel, carbide, aluminum alloy, and more.
Types Of Stamping Tool and die
Category | Type | Description | Features |
---|---|---|---|
Single-operation Die | Blanking Die | Used for material separation, such as blanking or punching | 1. Simple structure 2. Requires manual or mechanical transfer between stations 3. Longer production time 4. Higher scrap rate 5. Low cost |
Bending Die | Used to produce bending deformation in material, forming specific angles and shapes | ||
Drawing Die | Used to form hollow parts from sheet metal or change their shape and size | ||
Forming Die | Used for localized plastic deformation forming, such as bulging, flanging, etc | ||
Riveting Die | Used to connect parts into a whole using external force | ||
Compound Die | Compound Blanking Die | Performs blanking operation during a single press stroke. | 1. Compact mold structure, small size 2. Long manufacturing cycle 3. High precision and cost 4. Suitable for large-scale, high-precision stamping |
Compound Drawing Die | Performs drawing operation during a single press stroke | ||
Progressive Die | Progressive Die | Performs multiple operations in different stations during one press stroke. | 1. Dispersed processes, no minimum wall thickness issues 2. High die strengthEasy automation 3. Complex structure with high manufacturing cost but high production efficiency |
Multi-station Die | Allows different processes at multiple stations in one cycle |