In-Die Tapping Stamping
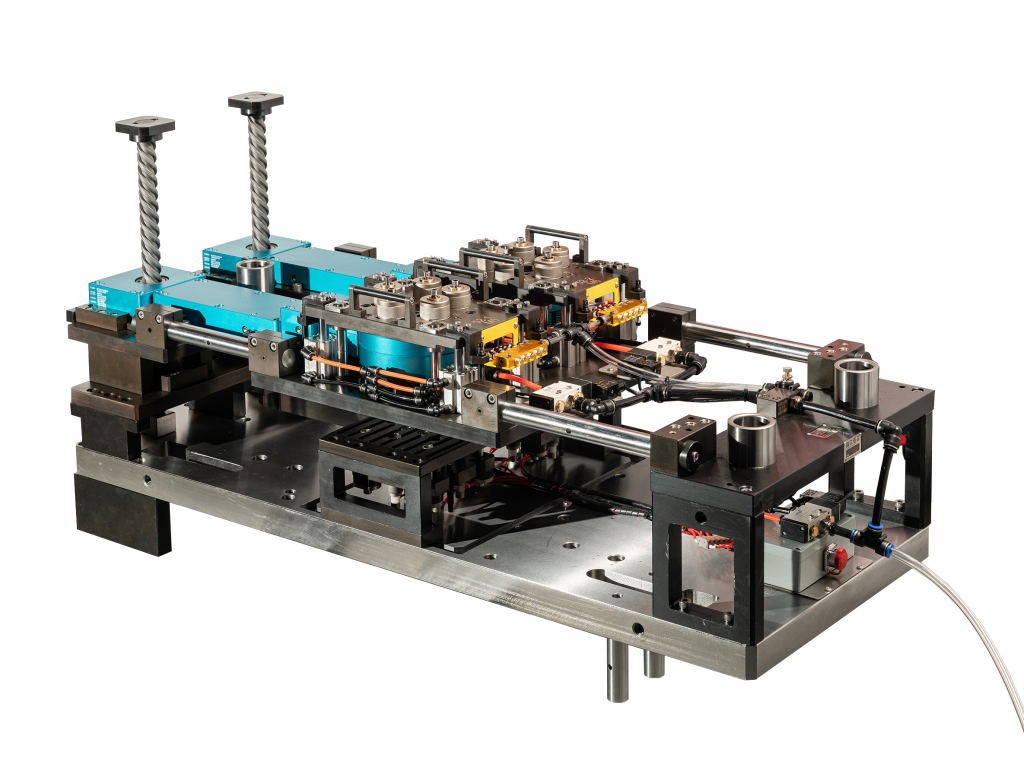
What is in-die tapping Stamping
In-die tapping is a manufacturing process that integrates thread tapping into stamping dies. It synchronizes punching, forming, and tapping operations during the stamping process, replacing the traditional two-step “stamping + secondary tapping” method. This process saves over 30% production time, reduces labor and equipment costs, and ensures precise alignment between threads and holes.
In-Die Tapping Stamping Process
During die design, tapping tools (taps) are integrated into the stamping die structure.
Process Flow:
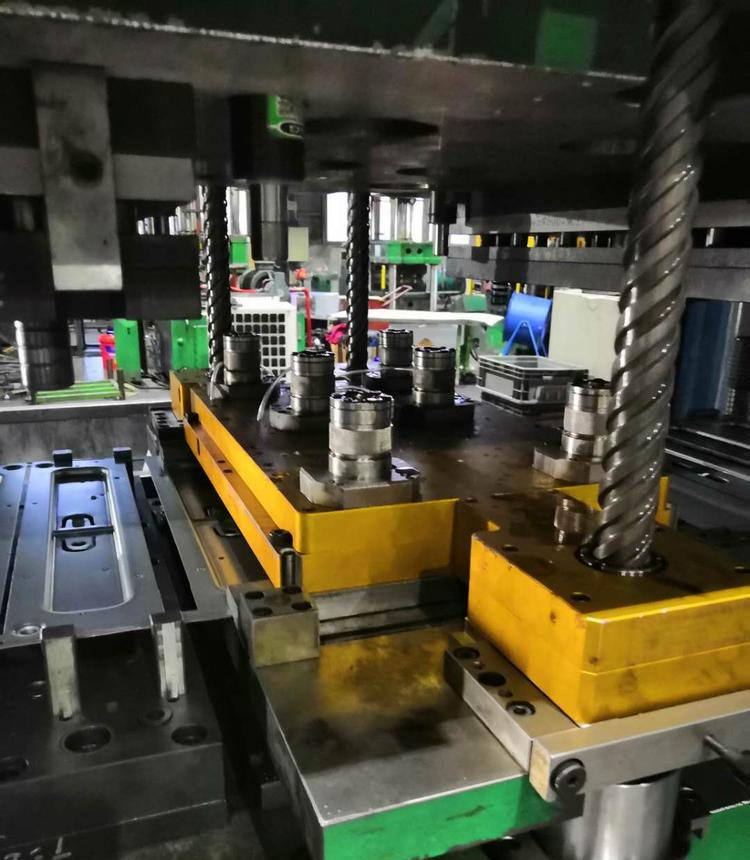
In-Die Tapping Stamping Die
Stamping die types are typically progressive dies or compound dies. Metaco has 100% in-house capabilities, from process analysis to tool manufacturing.
Metaco is fully collaborative, 1-on-1 engineering support from design to mass production.