How to Optimize Die Design for Metal Stamping
In metal stamping, die design is critical for ensuring efficient production, high-quality parts, and extended tool life. Proper die design reduces manufacturing costs, improves accuracy, and ensures consistent results. Here are the key factors to consider when optimizing die design.
Table of Contents
Material Selection
Tool steels and carbide are commonly used because of their wear resistance and ability to withstand the high pressures involved in stamping. The material selection depends on the type of metal being stamped, the production volume, and the expected wear and tear on the die. Dies need to handle repetitive stress while maintaining their shape and functionality.
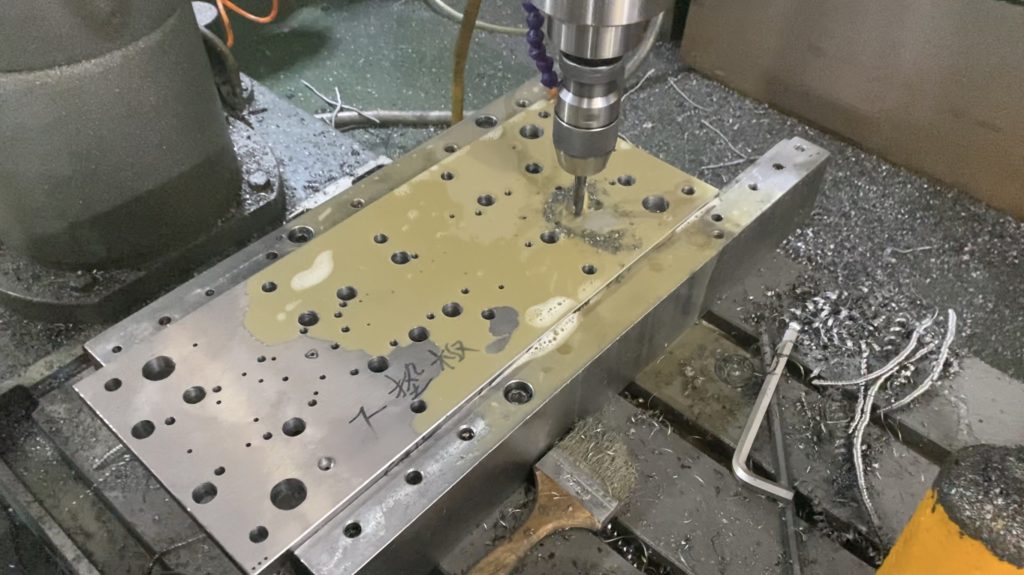
Die Geometry and Part Features
The die must guide the metal through the correct shape, preventing defects like distortion or cracks. A well-designed die has smooth transitions to ensure the metal flows properly. In more complex parts, using progressive dies allows for multiple operations within a single press stroke.
Clearance And Tolerances
Clearance refers to the gap between the upper and lower die components. If clearance is too tight, friction can cause excessive wear and deformation of both the die and the material. If it’s too wide, part dimensions can be inconsistent. Tight tolerances are especially important in industries like aerospace and automotive, where precision is critical.
Punch and Tooling Design
Punches and dies must be aligned to ensure uniform pressure distribution when forming or cutting parts. The punch should have appropriate radii and angles to reduce wear. For stamped parts with holes or cuts, the punch design determines the quality of the finished product. Tooling must also be selected based on material thickness and strength, with hardened inserts used for tough materials to ensure consistent performance over time.
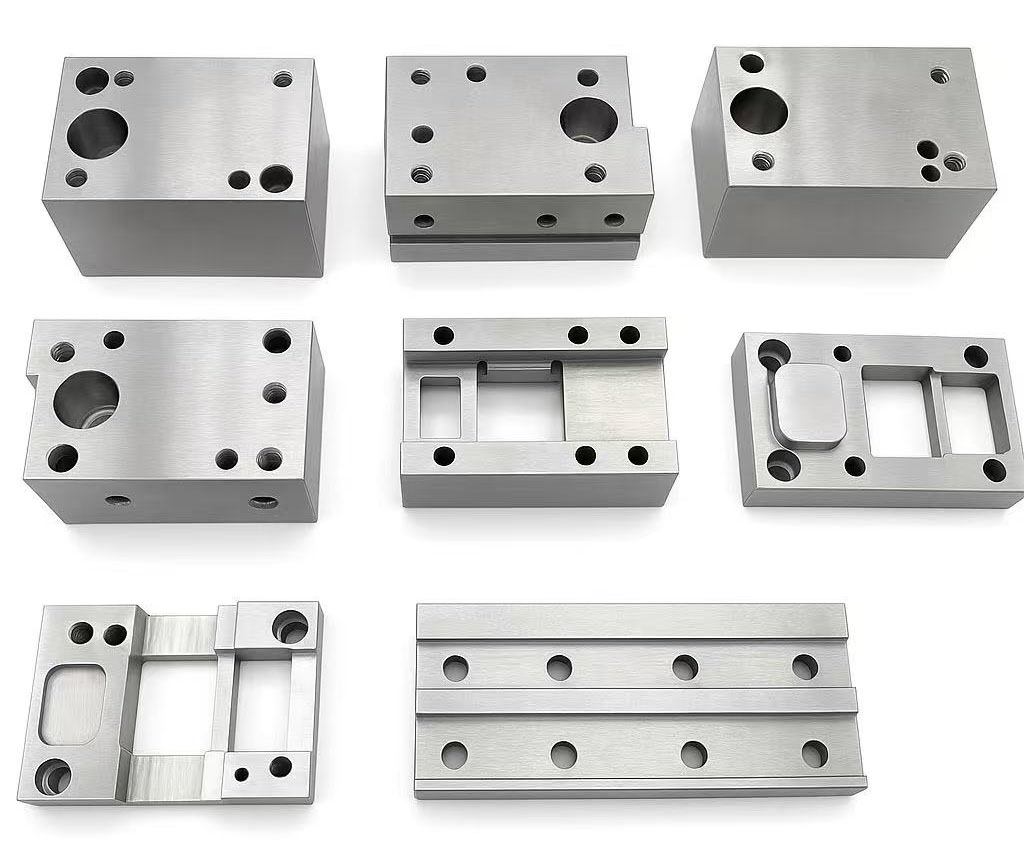
Die Maintenance and Automation
Regular maintenance is crucial to prolong die life and maintain high production standards. Monitoring systems are increasingly integrated into stamping processes, tracking wear and detecting potential issues. Automated systems can adjust die parameters to correct wear or misalignments before they affect part quality. This ensures consistent performance and reduces downtime for maintenance.