How to Engineer Low-Cost High-Volume Stamping Systems
Achieving cost efficiency in high-volume stamping demands precision engineering of three core elements: die architecture, material flow, and press dynamics. By redefining these components through advanced manufacturing principles, factories can produce complex parts at scale without compromising on unit economics.

Table of Contents
Die Architecture Optimization
Progressive dies integrate piercing, forming, and trimming operations within a single tool. This consolidation eliminates inter-station material handling, reducing cumulative tolerance stack-up to ±0.05mm across 10+ stations. Hardened guide pillars (HRC 62-64) paired with ball-bearing sleeves ensure alignment stability even at 1,200 strokes per minute. For ultra-thin materials (0.3-0.5mm), spring-loaded pressure pads maintain uniform blank holder force, preventing wrinkles during deep drawing.
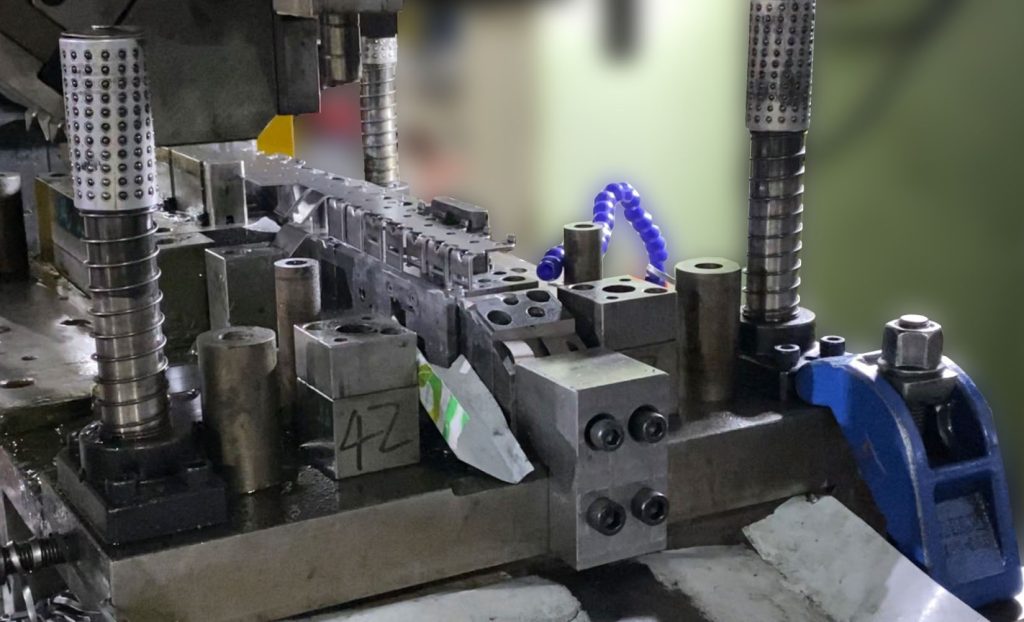
Material Flow Synchronization
Servo-driven feeders with closed-loop control synchronize strip advancement to press motion profiles. Photoelectric edge sensors detect material wander in real-time, triggering micro-adjustments through linear actuators (±0.02mm resolution). This system enables uninterrupted feeding of pre-coated steel coils while maintaining positional accuracy under 150spm cycling. Scrap minimization is further achieved through AI-optimized nesting, where parts are algorithmically arranged to yield 94%+ material utilization.
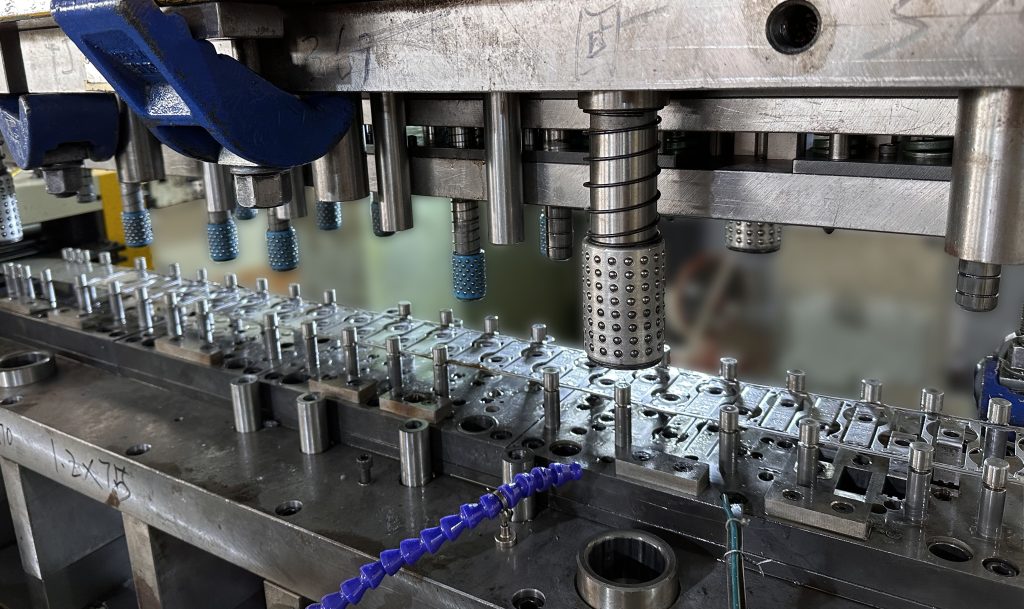