Common Defects in Powder Coating and Their Control Measures
Surface defects are a common quality control challenge in powder coating. Regardless of material quality or equipment performance, improper process parameters or deviations in operation can lead to issues in the final coating. These issues may affect surface appearance and reduce protective function, often resulting in rework and material waste.
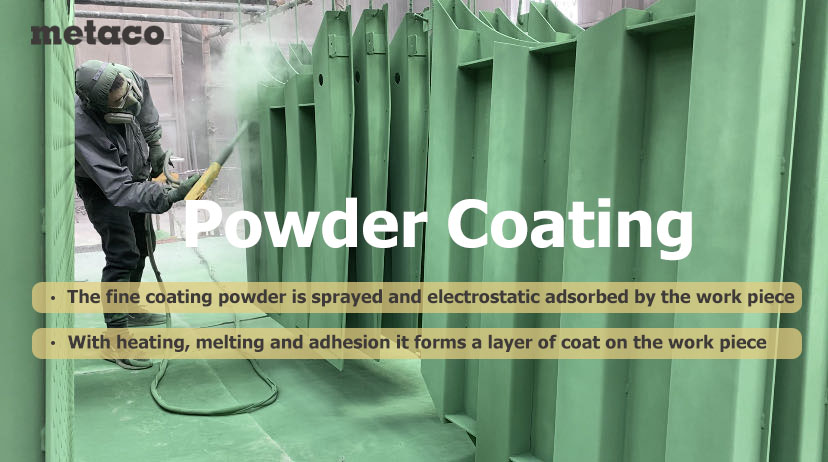
This article focuses on four typical surface defects: pinholes, poor adhesion, orange peel, and color variation. For each issue, potential causes are outlined and corresponding control measures are proposed.
Table of Contents
Pinholes
Pinholes appear as small holes on the coating surface, typically after curing. They are caused by moisture, oil, or trapped gases that fail to escape during heating, creating internal pressure and rupturing the surface.
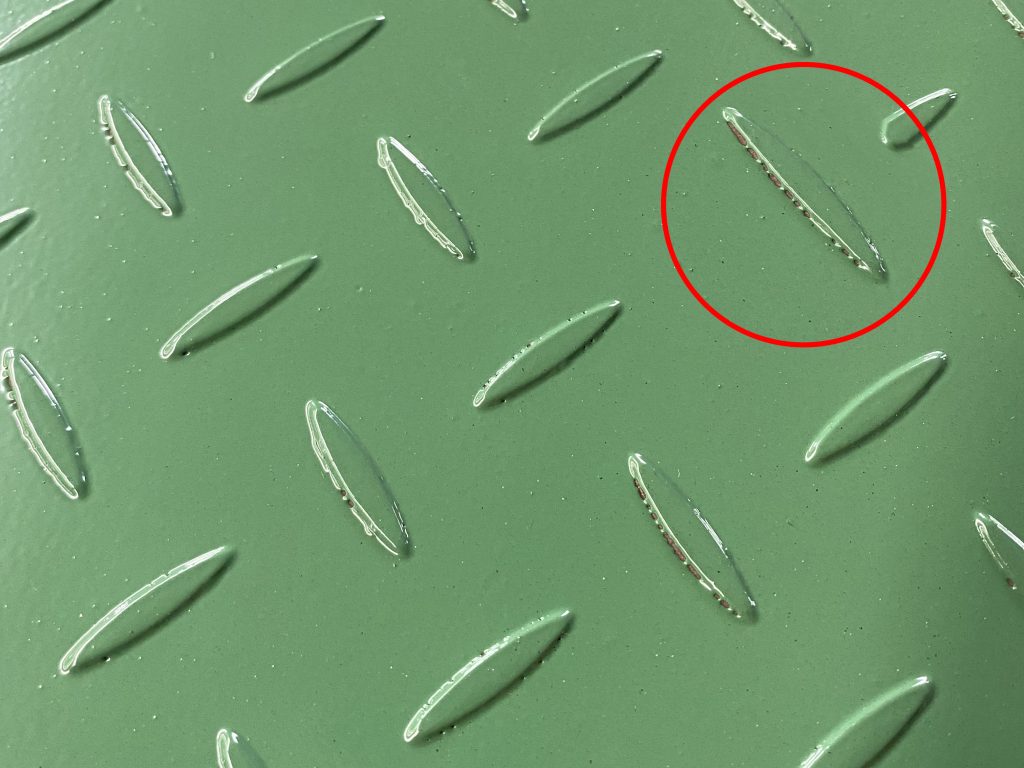
Common contributing factors include inadequate pretreatment, insufficient drying, excessive film thickness, and overly rapid heating. Control measures include:
Poor Adhesion
Poor adhesion is characterized by coating delamination or peeling, often visible during handling or transport. It is usually due to insufficient surface activation or incomplete curing of the powder.
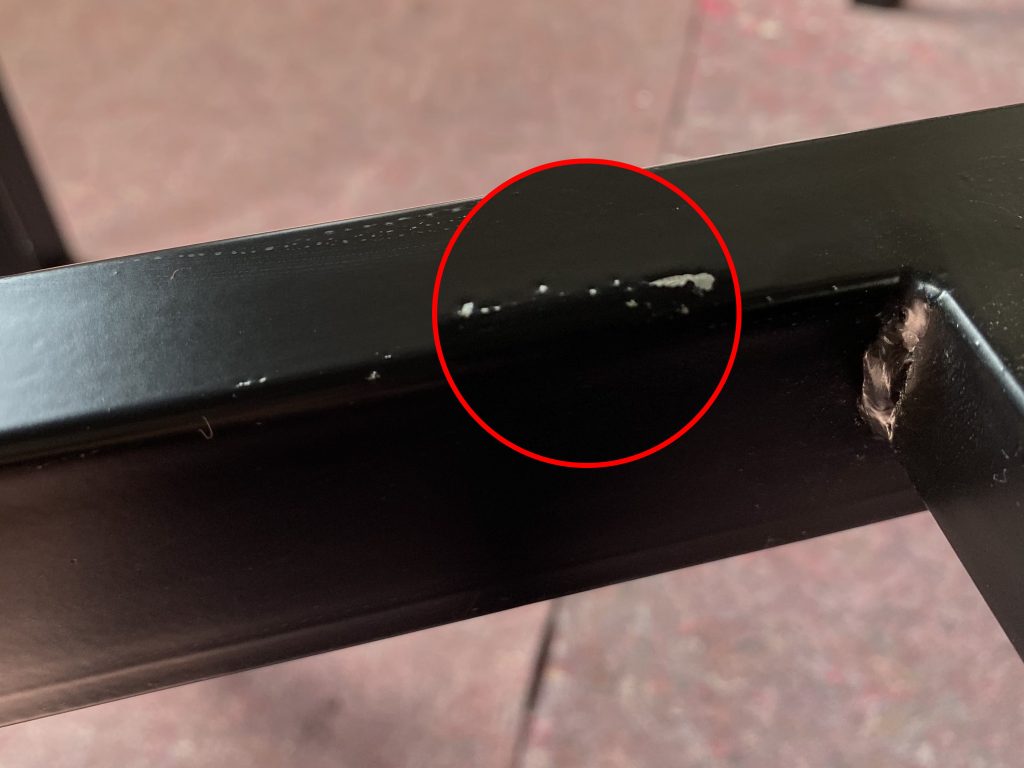
Typical causes include weak surface roughening, unstable phosphate film, or inadequate curing time and temperature. Solutions include:
Orange Peel
Orange peel refers to an uneven, textured surface caused by poor leveling during the melt phase. It may result from excessive film thickness, irregular powder size distribution, unstable substrate temperature, or inconsistent spray parameters.
Preventive actions include:
Color Variation
Color variation manifests as inconsistent coating appearance within or between batches. It is often related to changes in powder batch, process timing, or curing temperature. Environmental factors such as humidity and electrostatic stability can also influence the final result.
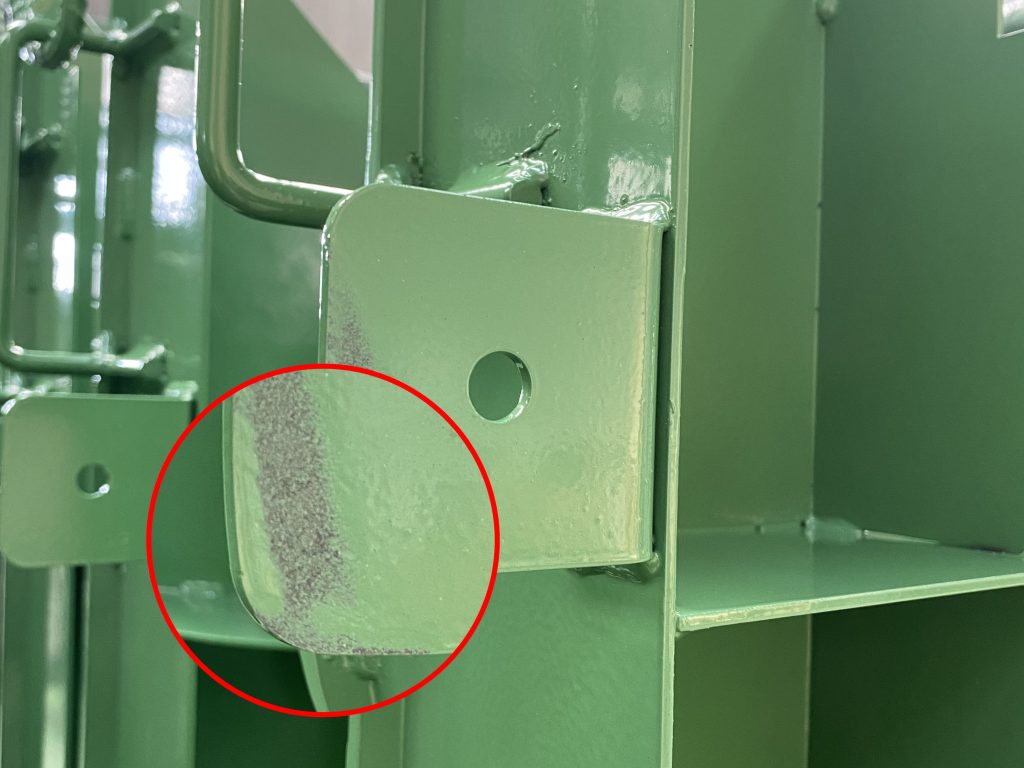
Recommendations include: