A Step-by-Step Guide to Tailored Metal Fabrication Solutions
When providing customized metal fabrication solutions for clients, it typically involves several steps to ensure their specific needs are met accurately. Below is a detailed process and approach, including key considerations for each stage:
Table of Contents
1. Understanding Customer Requirements
The first step in offering a customized solution is detailed communication with the client to ensure a complete understanding of their needs. This includes understanding the product’s use case, dimensional requirements, aesthetic design, and performance standards. By ensuring both parties have a unified understanding of the requirements, it provides a clear direction for subsequent design and fabrication.
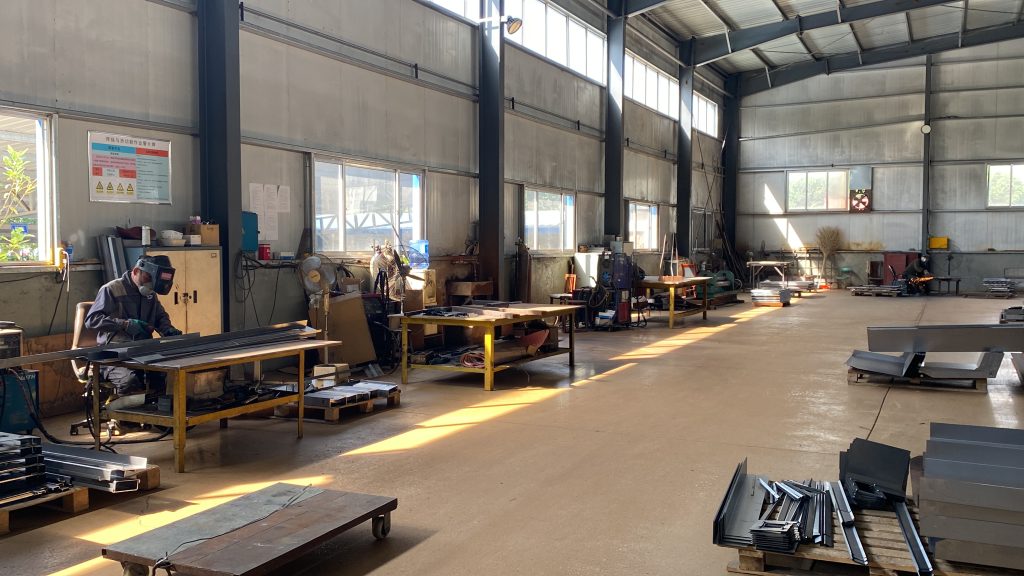
2. Selecting the Right Metal Material
Material selection is crucial in custom metal fabrication. Each type of metal has unique characteristics, such as steel’s high strength, stainless steel’s corrosion resistance, and aluminum’s lightness. Choosing the right material based on customer needs ensures the product performs excellently in terms of function and performance while also affecting cost and production timelines.
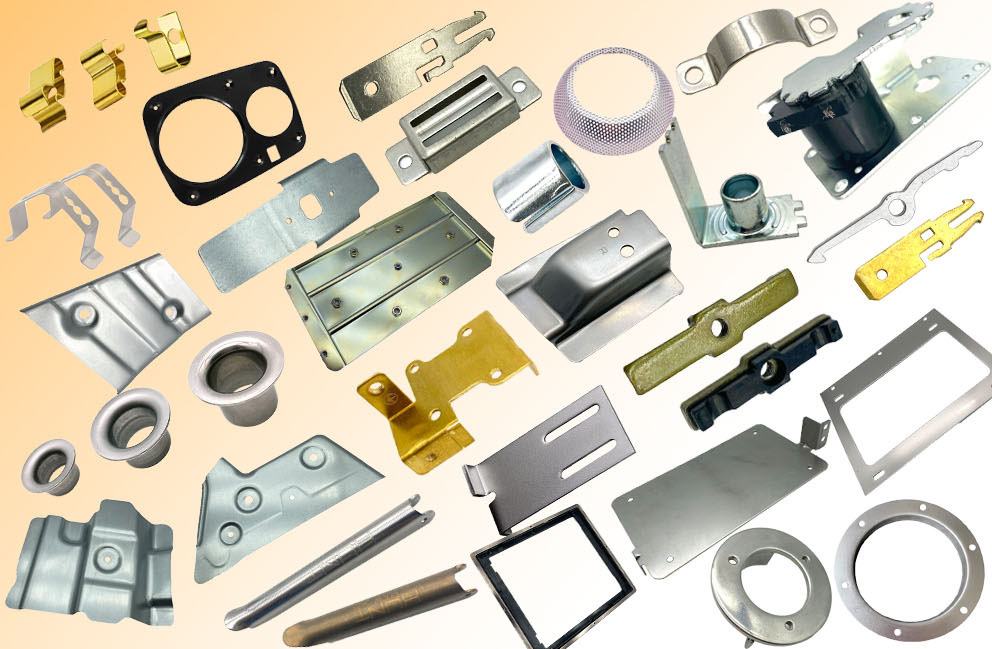
3. Design Optimization and Fabricability
Once customer requirements are defined, the design stage is critical. Using CAD (Computer-Aided Design) software to create a 3D model of the product ensures accurate dimensions and shapes, while also allowing potential fabrication issues to be foreseen during the design phase. Design optimization is not only about appearance and structure but also about considering the product’s manufacturability. This includes avoiding overly complex shapes and reducing processing steps to improve production efficiency and reduce costs.
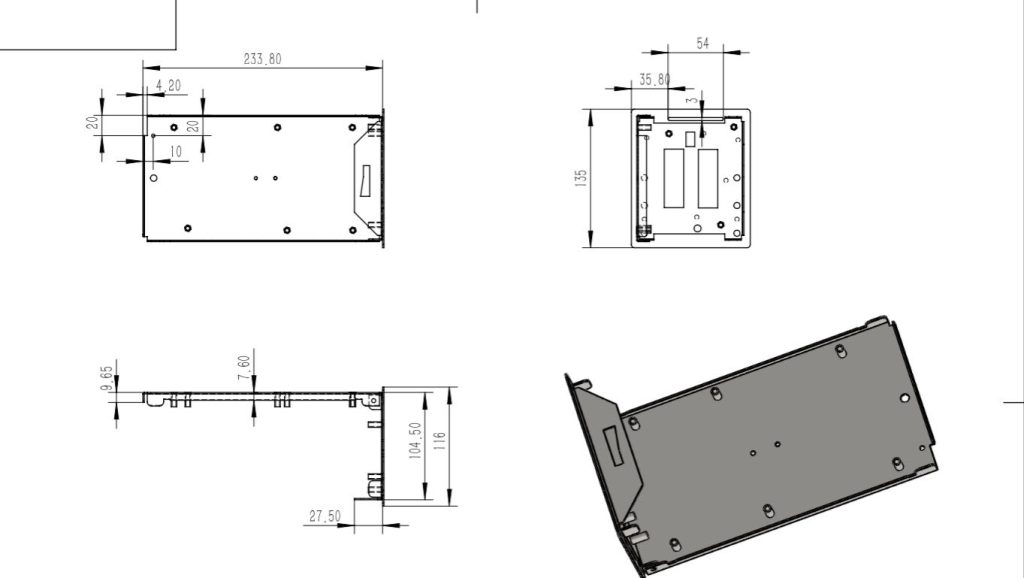
4. Selecting the Right Fabrication Process
Different metal fabrication processes greatly affect the quality and cost of the final product. Based on the design requirements, it is essential to choose the most appropriate fabrication methods, such as cutting, welding, stamping, or forming. For example, laser cutting is suitable for precise cuts, while water jet cutting is ideal for thicker materials. By selecting the right processes, production efficiency can be enhanced while ensuring the product meets the customer’s requirements.
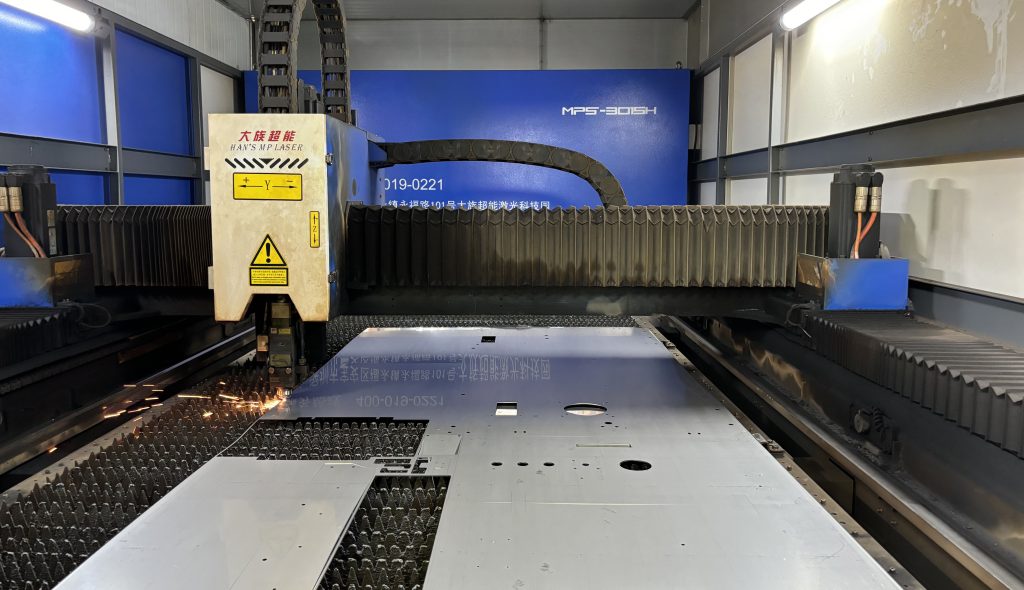
5. Surface Treatment and Functional Enhancement
Surface treatment not only improves the durability of the metal but also enhances the product’s functionality. For products that require corrosion resistance or an improved aesthetic, processes like electroplating, coating, or anodizing can be used. These treatments not only enhance the visual appeal of the product but also improve the metal’s protective properties, extending the product’s lifespan.
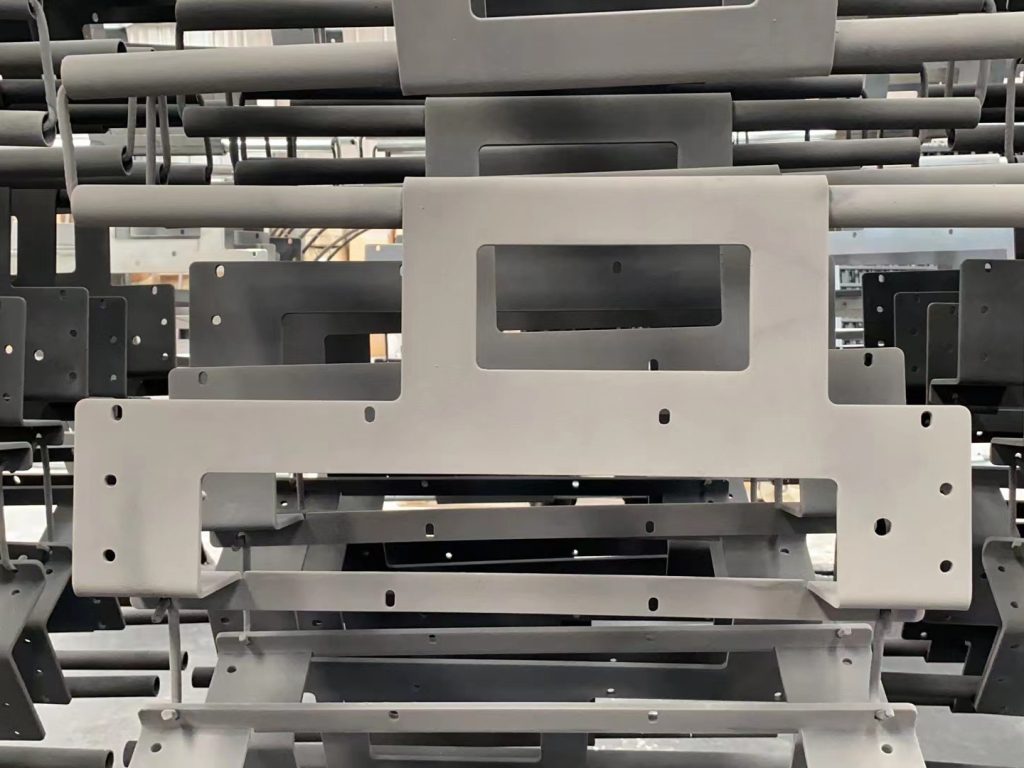
6. Cost-Effectiveness Analysis
Optimizing design and processes can effectively control costs. In custom metal fabrication, price is a significant concern for clients. By carefully selecting materials, optimizing fabrication methods, and streamlining production processes, manufacturing costs can be reduced. Additionally, considering the different needs of mass production versus small-batch production, adopting suitable production methods and automation technologies can increase efficiency and reduce unit costs.
7. Rapid Prototyping and Client Feedback
Prototyping is a crucial step to ensure the final product meets the client’s needs. Before mass production, providing a prototype allows the client to verify the design and feasibility of the fabrication process and make necessary adjustments. Prototype testing also helps both parties identify potential issues and address them promptly, ensuring the final product meets customer expectations.
8. Quality Control and Production
Strict quality control measures during production are essential to ensure the product meets the customer’s standards. From dimensional accuracy to material strength testing to surface finish, each stage needs thorough inspection. Continuous quality control ensures that every product meets predefined specifications and helps avoid defects during the production process.