Fixture Design and Positioning Techniques for Sheet Metal Butt Welding
In sheet metal butt welding, thin plates often suffer from misalignment, warping, and dimensional deviation due to their low rigidity. The primary causes usually lie in inadequate positioning structures or unstable clamping before welding.
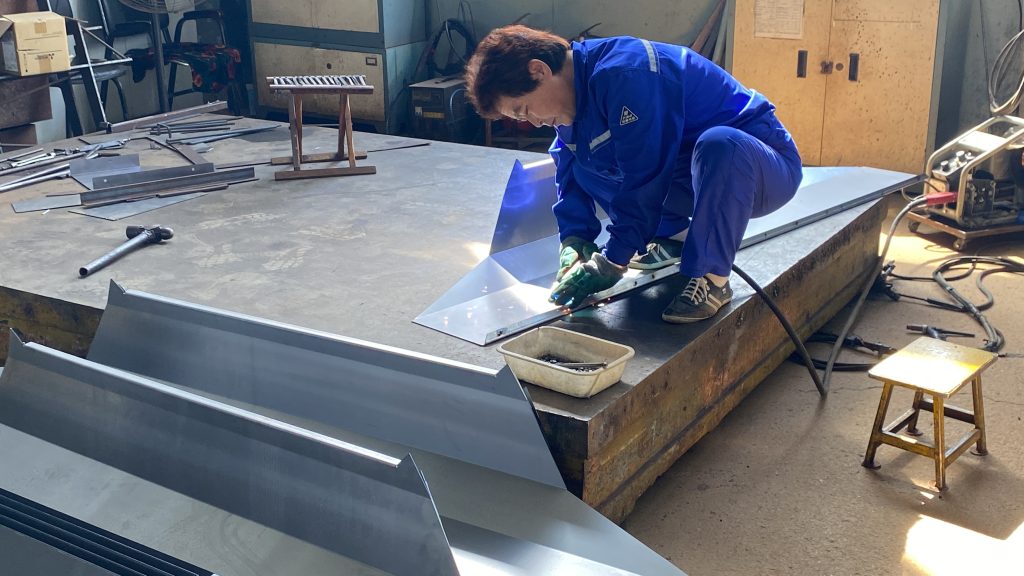
Table of Contents
Positioning Structures
The positioning structure must ensure proper alignment, contact, and restraint before welding. Common methods include side stoppers, locating pins with slots or holes, and edge overlaps. For standardized components, edge-mounted mechanical stops or alignment slots allow fast and repeatable positioning. In non-standard or flexible scenarios, spot welding combined with temporary clamps offers adaptability.
Joint Preparation
The joint edges must be straight and burr-free. A proper root gap between 0.2–0.5 mm is essential. Excessive gaps lead to incomplete penetration, while overly tight joints increase slag entrapment risks. A dry fit or mock assembly is recommended prior to welding to verify alignment consistency.
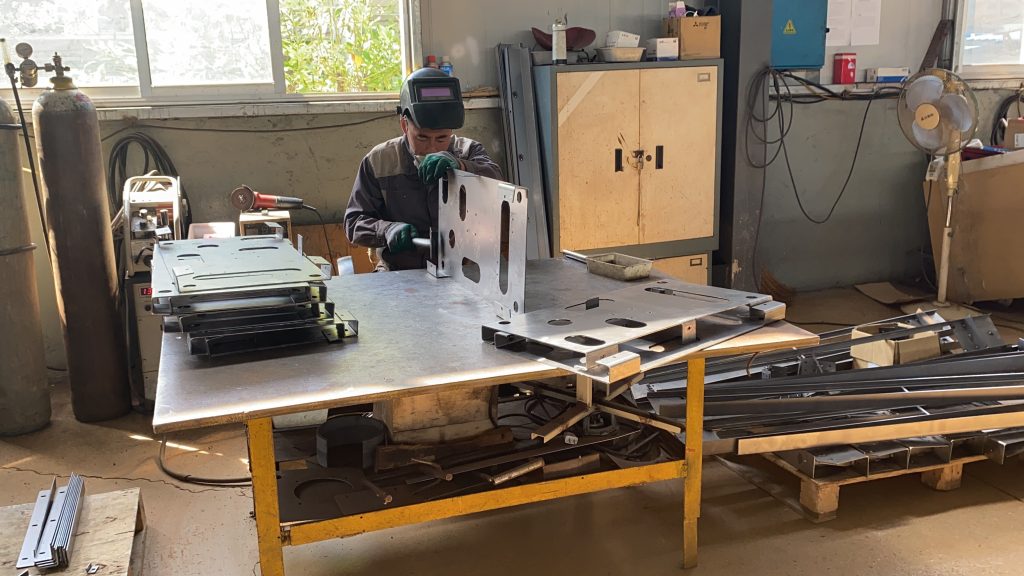
Clamping Methods
The clamping system must provide symmetric pressure across both sides of the weld seam. Clamps should avoid heat-affected zones to prevent indentation or material damage. Long panels require center support to prevent sagging or cumulative deformation. For thin plates, wide-surface clamps help distribute clamping force and reduce local stress. In batch production, pneumatic or adjustable fixtures significantly improve repeatability and efficiency.
Dimensional Control During Welding
Post-weld deviations can be compensated using counter-deformation, controlled weld sequences, or segmented welding. However, the root of dimensional accuracy still lies in precise positioning and rigid clamping during setup.
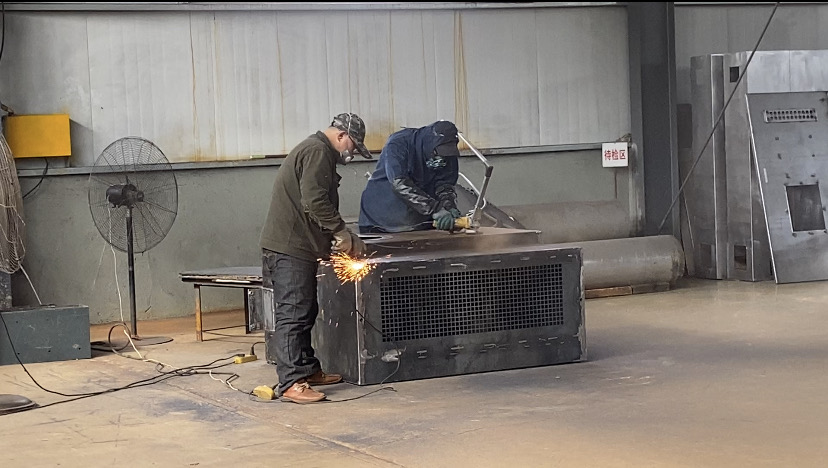
The quality of sheet metal butt welding depends less on the weld process itself, and more on the preparation beforehand. A well-designed positioning structure and a stable clamping system are fundamental to minimizing deformation and ensuring consistent weld quality.