Five Essential Factors in Stamping Die Design
Stamping dies are critical tools in high-volume metal forming. Their design directly affects part accuracy, production efficiency, and tool durability. A well-designed die reduces downtime, minimizes waste, and ensures consistent output. Below are five key factors every stamping die designer should consider.
Table of Contents
1. Material Selection and Heat Treatment
Die components must resist wear, deformation, and impact. Common choices include:
Heat treatment should match the function of each part. Punches and cutting sections need high hardness. Guide components require a balance of strength and toughness.
2. Proper Die Clearance and Process Analysis
Clearance between punch and die affects both part quality and die life. Too small, and the die wears quickly; too large, and the part may have burrs or poor tolerances.
For complex processes like deep drawing or bending, using forming simulations during design helps predict material flow, prevent wrinkles or cracks, and reduce trial runs.
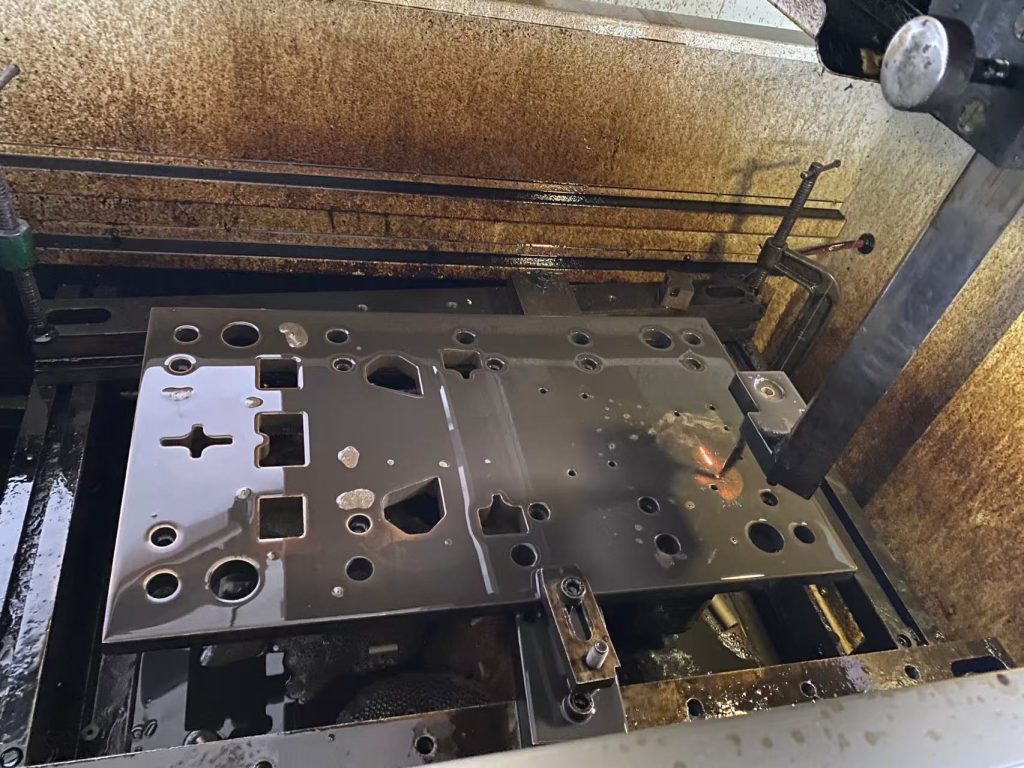
3. Standardization and Modular Design
A modular, standardized design improves both build and maintenance. Key practices include:
This not only reduces manufacturing lead time, but also simplifies repair and spare part management.
4. Ease of Maintenance and Durability
Dies should be designed for long-term use with simple maintenance procedures:
Proper design reduces unplanned downtime and extends tooling life.
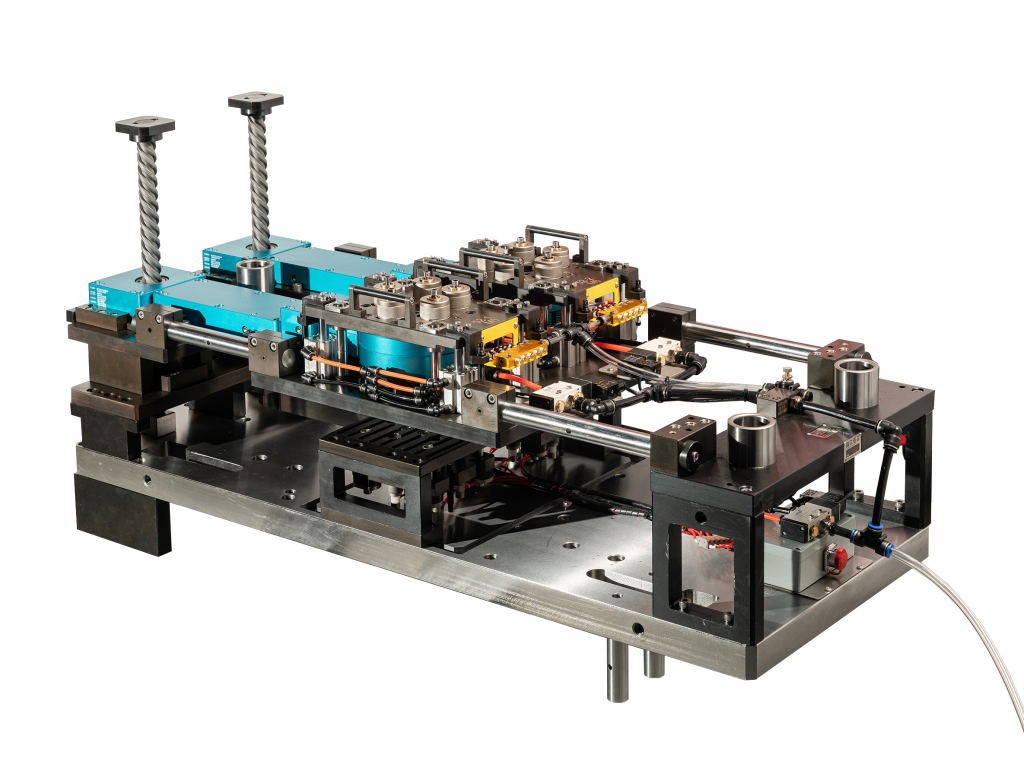
5. Safety and Manufacturability
Safety features protect operators and reduce risk. A few key elements:
Practical designs help control machining cost and improve overall tool quality.