Stamping Process Considerations for Metal–Plastic Composite Structures
Metal–plastic composite components typically consist of a stamped metal substrate combined with a molded or bonded plastic layer. The metal serves structural, thermal, or conductive functions, while the plastic provides insulation, damping, or geometric features. In most cases, the metal part is pre-formed by stamping before the plastic is applied.
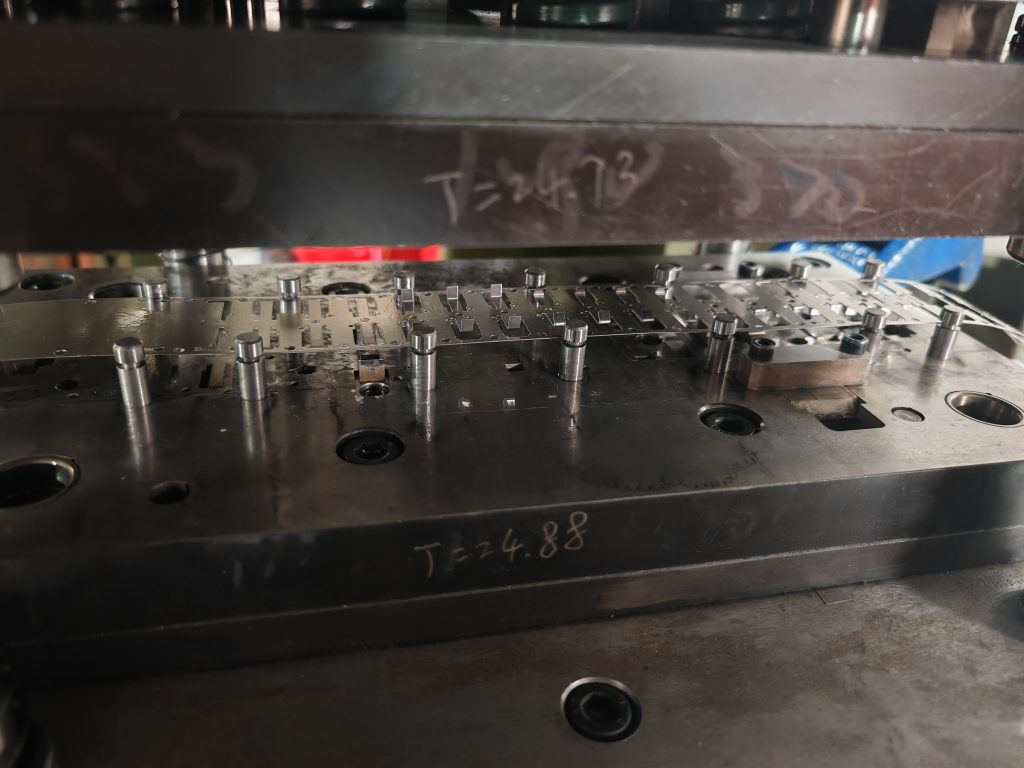
Table of Contents
Role of Stamping in the Composite Process
Stamping defines the initial geometry and functional features of the metal insert. Its responsibilities include:
Key Challenges in the Stamping Stage
1. Material Behavior Mismatch
Differences in thermal expansion, stiffness, and deformation characteristics between metal and plastic can cause internal stress or misalignment during overmolding. The stamped part must accommodate these factors within its forming tolerances.
2. Localized Deformation and Precision
Many composite structures require tight tolerances at local features such as locating tabs, press-fit bosses, or sealing edges. Complex forming geometries can lead to springback or localized wrinkling, especially in thin or multi-step parts.
3. Edge Quality
Since edges often interface directly with the plastic during overmolding, control of burrs, cracks, and shear marks is critical. Improper die clearance or tooling wear can result in defects that compromise bonding or insulation.
4. Tooling and Locating Requirements
Stamping dies for composite structures often include extra alignment or clamping features to support the downstream process. Tooling must account for orientation, flatness, and contact surface preparation.
5. Post-Stamping Distortion
Residual stress or incomplete forming can lead to flatness deviation, affecting fit in the injection mold. In some cases, additional forming steps or fixtures are required to stabilize the stamped shape before plastic application.