Integration of Metal Stamping and CNC Machining
Metal stamping is suitable for contour forming and preliminary structural processing of high-volume parts. It features fast forming speed and high material utilization. CNC machining is suitable for dimensional correction and functional secondary processing of critical areas, with high flexibility and precision control capabilities.
In the combined process, the sequence generally follows “pre-processing by stamping + precision finishing by CNC” to ensure that the preceding stamping process provides sufficient structural foundation, and that the subsequent CNC process can complete high-precision machining of critical dimensions, holes, or surface features based on defined datums.
Table of Contents
Process Coordination Between Stamping and CNC
Division of Contour Forming and Precision Dimensions
Stamping completes the overall contour and structural forming of the part, while CNC handles positioning holes, threaded holes, assembly surfaces, etc., where tighter tolerances are required.
Auxiliary Realization of Complex Structures
For parts with local features such as inclined surfaces, steps, or grooves, the main structure can be completed by stamping first, and then supplemented by CNC machining for details that cannot be achieved by the die.
Multi-Datum Precision Control
Using the locating datums formed by stamping as the reference for CNC machining can reduce clamping errors and improve overall dimensional consistency.
Surface Quality Handling and Functional Enhancement
For products with high requirements for surface smoothness or geometric accuracy, CNC can serve as a secondary finishing method to meet decorative or functional standards.
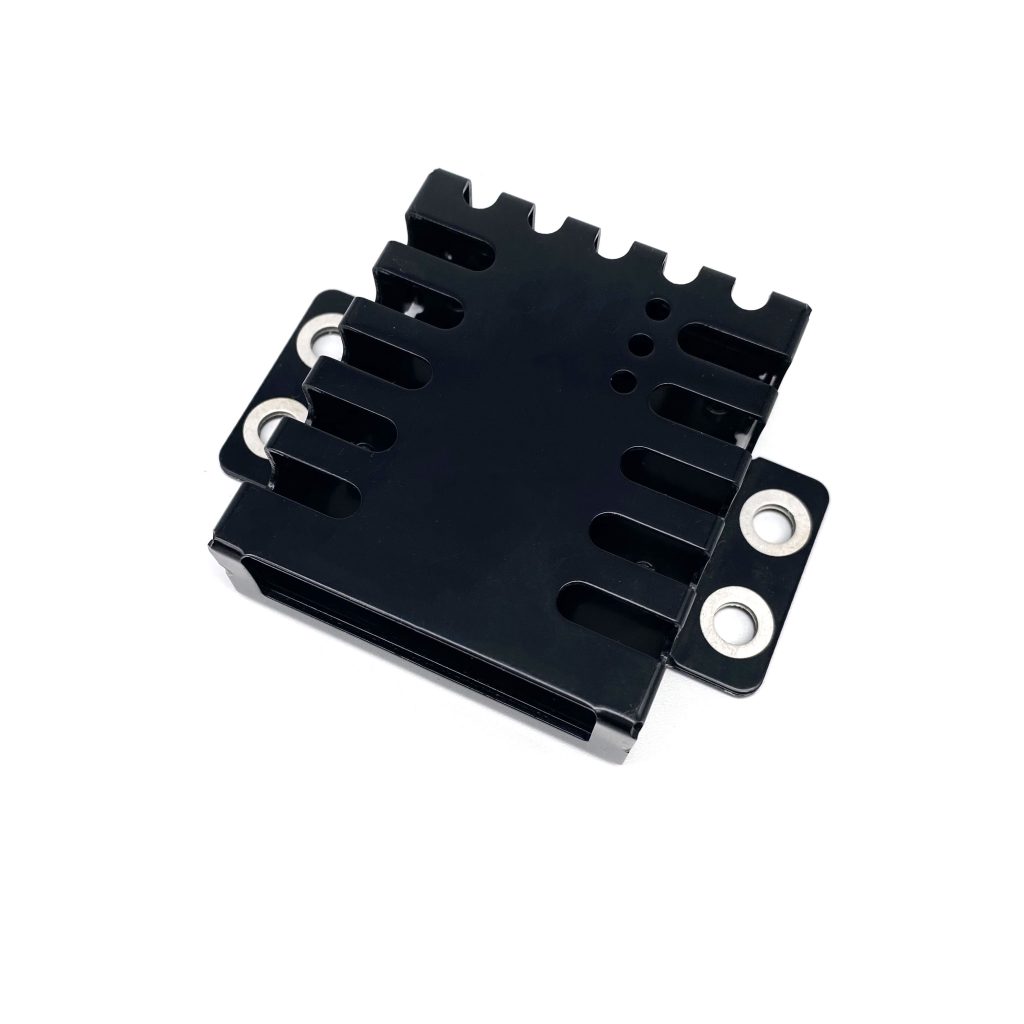
Key Control Points in Process Integration
When implementing a combined stamping and CNC process, the following technical control factors should be noted:
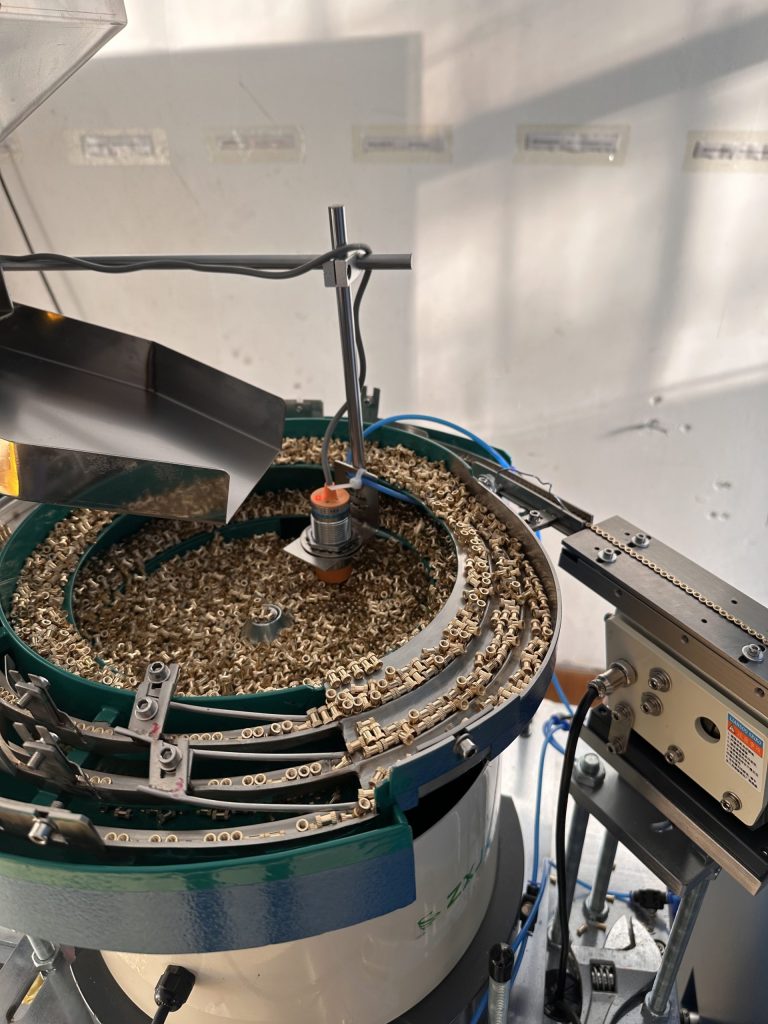