What Factors Affect the Cost of Making a stamping die and tool
Making a stamping die and tool is an essential process in many manufacturing industries, including automotive, aerospace, and electronics. The cost of making a tool can vary greatly depending on a range of factors. In this post, we will discuss the key factors that affect the cost of making a die.
Table of Contents
tool material
The type of material used to make the mold is a significant factor in determining the cost. The most commonly used mold materials are steel, aluminum, and copper. Steel is the most durable and long-lasting material, but it is also the most expensive. Aluminum is a less expensive option, but it has a shorter lifespan than steel. Copper is the least expensive but is only suitable for low-pressure applications.
tool size and complexity
The size and complexity of the mold also impact the cost. Larger and more complex dies require more time and resources to design, manufacture, and test, leading to a higher overall cost. The level of detail and precision required in the mold design also influences the cost, as it affects the time and skill required for tool making.
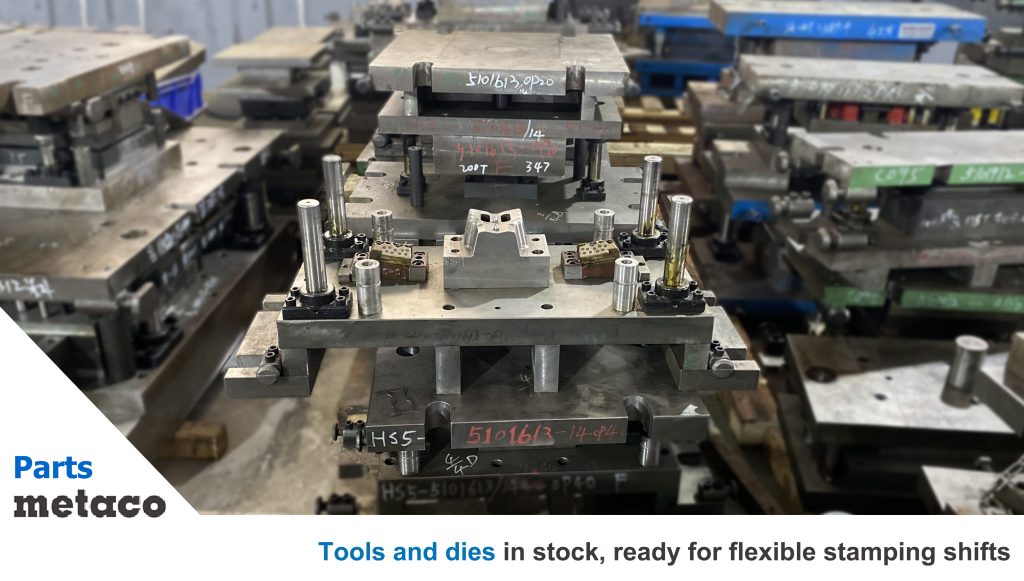
Number of cavities
The number of cavities in the mold affects the cost. A single-cavity die is less expensive to make than a multi-cavity die. The more cavities a mold has, the more complex and time-consuming the manufacturing process, leading to a higher overall cost.
Lead time
The lead time required for the mold-making process also impacts the cost. A shorter lead time often means higher costs, as it requires more resources to complete the mold-making process within a shorter timeframe.
Surface finish and texture
The surface finish and texture required in the mold can also impact the cost. A smooth and polished surface requires more time and skill to achieve, leading to a higher cost. A textured or rough surface is less expensive but may affect the quality of the final product.
Quantity
The quantity of parts to be produced from the mold also impacts the cost. A higher quantity often results in a lower cost per part, as the fixed costs of mold making can be spread out over a larger number of units.
The cost of making a mold can vary significantly depending on several factors, including the mold material, size and complexity, number of cavities, lead time, surface finish, and quantity. Manufacturers must carefully consider these factors when making decisions about mold making to ensure that they are making the most cost-effective and efficient choices.