Quality Control For Metal Stamping Fabrication
Quality Assurance (QA) testing refers to the process of inspecting and verifying that metal stamping products meet the required standards. The ability of metal stamping manufacturers to deliver parts on demand largely depends on the level and extent of the quality control inspection they provide.
At Metaco, we recognize the importance of quality control assurance for OEM metal stamping parts, which is why we have a comprehensive in-house quality inspection department and quality control assurance equipment. Here, you will learn how we ensure full-process quality control for custom metal stamping parts.
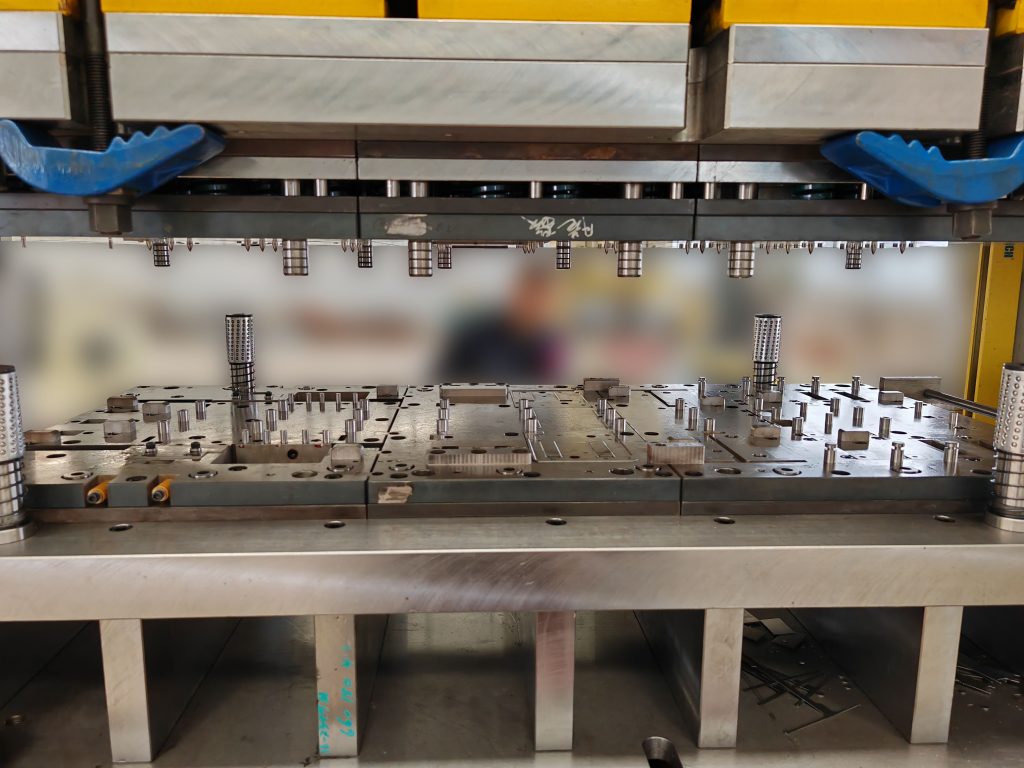
Quality Control in Die Evaluation
Quality Control in Sample Evaluation
Quality Control in Packaging
Quality Control For Metal Stamping Processes
Emphasis on Risk Management
Adherence to the IATF16949: 2016 quality management system, with certification handled by a third party and annual testing.
Quality Control Inspection Techniques
In-Die Inspection Systems
In-Die Measurement Systems
Optical Vision Systems
Functional Gauges and Custom Gauges
Statistical Process Control (SPC) Systems
Digital Measurement Machines with Metrology Software
Utilizing APQP for Quality Control Planning
The APQP process was developed by auto manufacturers and involves parts suppliers in every step of prototype and launch processes—from initial prototype to product launch and beyond. The APQP process monitors over 20 areas before production begins, including design robustness, design testing, quality inspection standards, and product packaging.
Quality Control for Secondary Services
The quality of parts requiring secondary processing is also under our strict supervision.Parts delivered by external manufacturs are inspected against standards before shipment to Metaco. Upon arrival at our factory, these components undergo a secondary inspection. Only those meeting our specifications are packaged and stored; parts failing to meet quality standards are returned for rework or remanufacturing. This ensures quality control throughout all stages of production.
At Metaco, everything we do, from the metal stamping process to secondary services, strictly adheres to our quality production standards. We offer custom precision metal stamping services for critical industries such as automotive, water treatment, and electronics, and have established a solid reputation.